Large Caliber HDPE Twisted Pipe Production Line: Everything You Need to Know
By:admin
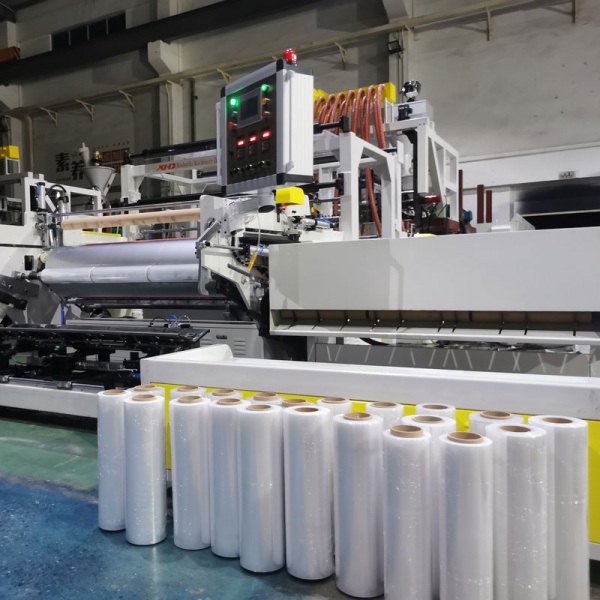
With the increasing focus on sustainable and long-lasting infrastructure, the demand for HDPE pipes has been steadily rising. These pipes are known for their exceptional strength, durability, and corrosion resistance, making them ideal for a wide range of applications including water and gas distribution, drainage systems, and industrial piping. The introduction of the HDPE large caliber twisted pipe production line is set to further bolster the capabilities of the company in meeting the evolving needs of its customers.
The production line incorporates cutting-edge technology and innovative design features to ensure the seamless manufacture of large caliber HDPE pipes. This includes advanced extrusion and twisting processes that enable the production of pipes with superior performance characteristics. The use of high-quality HDPE materials further ensures the longevity and reliability of the pipes, even in the most demanding environments.
In addition to the technical aspects, the company's strong commitment to quality and customer satisfaction sets them apart in the industry. With a focus on continuous research and development, the company has been able to consistently deliver innovative solutions that exceed the expectations of their customers. The introduction of the HDPE large caliber twisted pipe production line is a testament to this commitment, as it represents a significant leap forward in the capabilities of the company to address the growing market demand for high-quality HDPE pipes.
Furthermore, the company's extensive experience and expertise in the field of plastic machinery manufacturing enables them to provide comprehensive support to their customers. From initial consultation and planning to installation, training, and after-sales service, the company is dedicated to ensuring the success of their customers' projects. This holistic approach to customer service has been a key factor in the company's continued success and standing as a trusted partner in the industry.
In line with the company's ethos of sustainability and environmental responsibility, the new HDPE large caliber twisted pipe production line is designed to optimize energy and resource usage while minimizing waste. This is in line with the global trend towards green manufacturing practices and aligns with the company's commitment to reducing its environmental footprint.
As the demand for HDPE pipes continues to grow, the introduction of the HDPE large caliber twisted pipe production line marks a significant milestone for the company. With its advanced technology, unwavering commitment to quality, and comprehensive customer support, the company is well-positioned to meet the evolving needs of the market and lead the way in the manufacturing of high-quality HDPE pipes.
In conclusion, the launch of the HDPE large caliber twisted pipe production line represents a significant advancement in the capabilities of the company to meet the increasing demand for high-density polyethylene pipes. With its innovative technology, dedication to quality, and customer-centric approach, the company is poised to set new standards in the industry and further solidify its position as a leading manufacturer of plastic machinery. This development is not only a testament to the company's commitment to innovation and excellence but is also a positive sign for the industry as a whole.
Company News & Blog
Manufacturer and Supplier of PVC Pipe Extruder - Factory Direct Prices
Leading PVC Pipe Extruder Manufacturer Expands Global ReachChampion Machinery, a renowned manufacturer, and supplier of top-quality PVC pipe extruders, is making significant strides in expanding its global market presence. With a strong focus on international markets, Champion Machinery has been actively establishing a global agent network and localizing its brand to meet the growing demand for its superior products worldwide.The company's commitment to providing high-quality PVC pipe extruders has earned it a solid reputation in the industry. Its state-of-the-art manufacturing facilities located in China are equipped with advanced technology to produce a wide range of top-quality PVC pipe extruders that meet various industrial and commercial needs.Champion Machinery's PVC pipe extruders are built with precision engineering and are known for their exceptional efficiency, durability, and ability to produce PVC pipes of different sizes and specifications. Whether for water supply, sewage systems, or other applications, the company's PVC pipe extruders offer a reliable and efficient solution.The company's dedication to exceptional customer service is evident in its team of experienced technicians who are readily available to provide expert advice and support to customers. This commitment to customer satisfaction has positioned Champion Machinery as a trusted partner for businesses seeking reliable and high-performance PVC pipe extruders.In addition to its commitment to quality and customer service, Champion Machinery also offers an extensive product system that includes Vacuum Forming, Recycling Plastic, Sheet Film Line, Blow/Injection Molding Machines, EPE Foam Machines, Hydraulic Cutting Machines, Air Compressors, Screw Compressors, Chillers, Hopper Dryers, Crushers, Mixers, and Auto Loaders. This comprehensive product range provides intelligent integrated system solutions for Material Feeding, Air Supply, Water Supply, and Power Supply.With a strong technical strength and supply chain advantages, Champion Machinery is able to efficiently meet customized demands, further solidifying its position as a leading PVC pipe extruder manufacturer and supplier.Furthermore, the company's dedication to international markets is evident in its efforts to establish a global agent network, enabling it to effectively reach customers around the world. By promoting and localizing the Champion brand, the company has expanded its presence across Asia, Europe, Oceania, North and South America, Africa, and the Middle East.To further strengthen its global presence, Champion Machinery has engaged in face-to-face communication with customers overseas, fostering improved mutual understanding and enhanced service delivery. This direct engagement with customers has proven instrumental in strengthening relationships and providing tailored solutions based on specific market needs.Moreover, Champion Machinery's commitment to innovation and continuous improvement has enabled the company to stay ahead of the curve in a rapidly evolving industry. The company's investment in cutting-edge technology and research and development has resulted in products that are not only high-performing but also aligned with industry standards and regulations.As part of its global strategy, Champion Machinery remains dedicated to providing reliable, efficient, and high-quality PVC pipe extruders to meet the needs of businesses worldwide. With a strong emphasis on customer satisfaction, technical expertise, and product innovation, the company continues to set new standards in the PVC pipe extrusion industry.In conclusion, Champion Machinery's expansion into global markets signifies its unwavering commitment to providing superior products and services to customers worldwide. As the demand for high-quality PVC pipe extruders continues to grow, Champion Machinery stands poised to meet the evolving needs of businesses across various industries, setting a benchmark for excellence in the PVC pipe extrusion industry.
Second-Hand Horizontal Injection Molding Machine Available for Sale in 2011 - Reyid
Reyid, the leading provider of industrial equipment, accessories, and industrial engineering solutions in China, has announced that it has a Used Chenhsong Super Master Injection Molding Machine available for sale. The Super Master series is a high-performance injection molding machine ideal for producing high-precision plastic products. The machine is in excellent working condition, having been manufactured in 2011, and is ideally suited for companies in the plastic manufacturing industry looking to expand their capacity.The machine is a horizontal injection molding machine and can process thermoplastics efficiently. It is also fully automatic, which ensures that the operator can focus on other crucial aspects of the manufacturing process. The machine has a 160 injection weight and an injection rate of 140, making it ideal for high production requirements. It has a clamping force of 500KN-16000KN, which facilitates the production of larger and more complex plastic products.The Super Master Injection Molding Machine has an opening stroke of 280-1500mm and runs on a 50Hz power supply. The machine's horizontal orientation makes it advantageous in manufacturing products that require a consistent flow of materials. It also facilitates faster and more accurate production processes.The Used Chenhsong Super Master Injection Molding Machine available for sale by Reyid provides companies in the plastic manufacturing industry with an opportunity to expand their production capacity. This machine is an excellent investment for both large and small-scale manufacturers looking to produce high-quality products efficiently. The Super Master Series Injection Molding Machine is known for its consistency, precision, and high-performance capabilities, which make it an excellent option for companies that demand high-quality production output.Reyid is a reliable provider of industrial equipment in China, with a reputation for delivering quality products and exceptional customer service. It provides a wide range of solutions for businesses in different industries, including automation, robotics, and industrial engineering. With Reyid, businesses can be assured of receiving the best equipment for their specific needs, and with the after-sale support provided, their investment will be further protected.By offering the Used Chenhsong Super Master Injection Molding Machine for sale, Reyid has further solidified its position as a leading provider of industrial equipment solutions in China. With this machine, businesses can expand their production capacity efficiently and effectively while maintaining the same high standards of quality.In conclusion, the Used Chenhsong Super Master Injection Molding Machine available for sale by Reyid is an excellent investment for businesses seeking to expand their production capacity. It is a high-performance machine that is in excellent working condition and will facilitate precision molding of high-quality plastic products. As Reyid continues to provide quality equipment solutions to businesses in different industries, its reputation as a reliable provider of industrial equipment in China will only continue to grow.
High-Quality Plastic Cover Making Machine - Factory Direct Sale
The global market for plastic cover making machines is growing, and companies are looking for reliable and efficient machines to meet their production needs. Champion Machinery, a leading manufacturer and supplier based in China, has positioned itself as a key player in this industry, offering high-quality and advanced Plastic Cover Making Machines at competitive prices.Champion Machinery has established a strong global agent network, promoting the Champion brand and localizing its services to cater to the diverse needs of international markets. With a presence in Asia, Europe, Oceania, North and South America, Africa, and the Middle East, Champion Machinery has proven its commitment to serving customers worldwide.The company's main products include a range of machinery designed for various applications, including Vacuum Forming, Recycling Plastic, Sheet Film Line, Blow/Injection Molding Machines, EPE Foam Machines, Hydraulic Cutting Machines, and Air Compressor/Screw Compressor/Chiller/Hopper Dryer/Crusher/Mixer/Auto Loader all in 1 intelligent integrated system solutions for Material Feeding, Air Supply, Water Supply, and Power Supply. Champion Machinery leverages its technical strength and supply chain advantages to efficiently meet customized demand, providing comprehensive solutions for businesses in the plastic manufacturing industry.One of the standout products offered by Champion Machinery is the Plastic Cover Making Machine, which is specifically designed to produce high-quality plastic covers for a wide range of products. Made from high-grade materials and utilizing advanced technology and innovative designs, these machines are built to withstand the rigor of daily use and guarantee long-lasting performance.The Plastic Cover Making Machine is user-friendly, featuring a simple interface for easy operation. It is also highly versatile, capable of producing covers with different materials, sizes, and shapes, catering to the diverse needs of businesses across various industries. Whether a business needs a machine for small-scale or large-scale production, Champion Machinery offers reliable and efficient solutions.In addition to providing top-quality machinery, Champion Machinery also offers excellent after-sales support and technical assistance to ensure that its clients receive maximum benefits from their investments. The company's exceptional customer service extends to comprehensive training and ongoing technical support, ensuring that businesses can operate their machinery with confidence and efficiency.Customer reviews of the Plastic Cover Making Machine reflect high satisfaction with its performance and reliability. Customers have praised the machine for its ability to handle high-volume manufacturing, its ease of operation, and its low maintenance requirements. The machine is also lauded for its versatility and its state-of-the-art technology, which ensures precise cutting, shaping, and welding of plastic materials. Overall, the Plastic Cover Making Machine is seen as a great investment for businesses looking to streamline their manufacturing processes and increase their production capacity.Champion Machinery's dedication to providing top-quality machinery and comprehensive support services has positioned the company as a leading manufacturer and supplier in the plastic manufacturing industry. With a strong global presence and a commitment to meeting the needs of its customers, Champion Machinery continues to be a trusted partner for businesses seeking reliable and efficient solutions for their production needs.In conclusion, Champion Machinery's commitment to innovation, quality, and customer satisfaction has solidified its position as a leading manufacturer and supplier of Plastic Cover Making Machines. With a global network of agents and a strong presence in key international markets, the company continues to serve businesses worldwide, offering advanced machinery and comprehensive solutions for the plastic manufacturing industry.
High-Density Polyethylene: A Guide to CNC Machining and Applications
CNC HDPE, a leading manufacturer of high-density polyethylene (HDPE) products, has recently expanded its product line to include a new range of cutting-edge HDPE materials. The company has invested heavily in research and development to create these innovative materials, which offer superior performance and durability compared to traditional HDPE products. This latest development underscores CNC HDPE's commitment to providing its customers with the highest quality materials for their specific needs.HDPE is a versatile material that is widely used in a variety of industries, including construction, packaging, and agriculture. It is known for its strength, chemical resistance, and overall durability. However, CNC HDPE has taken these characteristics to the next level by introducing a new line of HDPE materials that are even more robust and long-lasting.One of the key features of CNC HDPE's new materials is their improved impact resistance. This makes them ideal for applications where the material will be subjected to high levels of stress or wear and tear. Additionally, the new materials offer enhanced resistance to harsh chemicals, making them suitable for use in environments where traditional HDPE materials may not be suitable.Moreover, CNC HDPE's new HDPE materials are designed to be easily machinable, making them a perfect choice for customers who require precision components. The materials can be easily shaped and formed to meet the specific requirements of a wide range of applications, from industrial machinery components to intricate consumer products.In addition to their superior performance characteristics, CNC HDPE's new materials are also more environmentally friendly than traditional HDPE products. The company has invested in developing materials that are fully recyclable, reducing the environmental impact of the manufacturing process and providing a sustainable solution for its customers.CNC HDPE's dedication to innovation and quality is reflected in its state-of-the-art manufacturing facilities. The company's production processes are designed to ensure the highest standards of quality and consistency in every product it manufactures. With a focus on precision and efficiency, CNC HDPE is able to deliver high-quality materials to its customers in a timely manner.The company's commitment to customer satisfaction is also evident in its dedication to providing exceptional service and support. CNC HDPE's team of experts is available to assist customers with selecting the right materials for their specific needs and to provide technical guidance throughout the manufacturing process. This level of support ensures that customers can confidently choose CNC HDPE as their trusted partner for all their HDPE material needs.CNC HDPE's new line of cutting-edge HDPE materials represents the company's ongoing dedication to pushing the boundaries of what is possible with this versatile material. By investing in research and development, CNC HDPE continues to set the standard for quality and innovation in the HDPE industry. This latest development is a testament to the company's commitment to meeting the evolving needs of its customers and providing them with the best possible solutions for their specific applications.As CNC HDPE continues to expand its product line and enhance its manufacturing capabilities, customers can expect even more groundbreaking developments in the future. With a focus on quality, performance, and sustainability, CNC HDPE is poised to remain a leader in the HDPE industry for years to come.
Affordable and Reliable Second Hand Pet Bottle Making Machine from China
Champion Machinery Expands its Reach with Second-Hand Pet Bottle Making MachinesAs a leading manufacturer in China, Champion Machinery has been dedicated to providing high-quality machines at wholesale prices. The company recently introduced a best-value, second-hand pet bottle making machine in the market, offering a cost-effective and reliable solution for businesses seeking to optimize their manufacturing process while minimizing expenses.The second-hand pet bottle making machine has been thoroughly inspected and refurbished to ensure optimum performance and longevity. With advanced technology and robust construction, the machine can efficiently produce high-quality pet bottles for various industries, including water, beverage, and household cleaning products.The company's second-hand pet bottle making machine is specifically designed to cater to the demands of small and medium-scale industries. It features a user-friendly interface and automated controls, making it easy to operate and reducing the need for extensive manual labor. Additionally, the machine incorporates eco-friendly features such as energy-efficient mechanisms and reduced material wastage, aligning with the company's commitment to environmental responsibility.Customer satisfaction is a top priority for Champion Machinery, and the company offers technical support and guidance throughout the purchase process, ensuring that customers can make the best out of the machine. The experienced technicians provide thorough inspection, servicing, and support to ensure optimal performance and minimal downtime.The decision to offer second-hand pet bottle making machines aligns with Champion Machinery's global strategy and increased efforts on exploring international markets. The company's global agent network has been established to promote and localize the Champion brand, with footprints all over the world including Asia, Europe, Oceania, North and South America, Africa, and the Middle East.Champion Machinery's main products include a "many" Product System, which refers to the 6 Series of Products including Vacuum forming, Recycling plastic, Sheet film Line, Blow/injection molding machine, EPE foam machine, Hydraulic cutting machine, Air compressor/Screw compressor/Chiller/Hopper dryer/Crusher/Mixer/Auto loader all in 1 intelligent integrated system solutions for Material Feeding, Air Supply, Water Supply, and Power Supply.The company's technical strength and supply chain advantages enable Champion Machinery to efficiently meet customized demands, providing businesses with comprehensive solutions for their manufacturing needs.The introduction of second-hand pet bottle making machines reflects Champion Machinery's commitment to offering reliable and affordable solutions for businesses seeking quality and cost-effectiveness. By harnessing the potential of the second-hand pet bottle making machine, businesses can gain a competitive edge in the market and streamline their production processes.In conclusion, Champion Machinery's second-hand pet bottle making machine presents businesses with an opportunity to invest in a reliable production tool while benefiting from exceptional customer service and cost-effectiveness. Contact Champion Machinery today to explore the numerous advantages offered by the second-hand pet bottle making machine and discover why the company is the go-to choice for businesses seeking reliable and affordable manufacturing equipment.
Buy High-Quality Plastic Moulding Machine on OLX - Wholesale Deals from China
Champion, a leading manufacturer and supplier of plastic moulding machines based in China, is making waves in the international market with its commitment to quality and innovation. With a strong focus on global expansion, Champion has established a robust network of agents around the world and actively promoted its brand on a localized level.The company has been actively seeking out new opportunities in international markets, and its efforts have paid off as its footprints have extended to Asia, Europe, Oceania, North and South America, Africa, and the Middle East. This global presence has allowed Champion to engage in face-to-face communication with customers overseas, ultimately leading to improved mutual understanding and enhanced service delivery.Champion's main product lineup includes a diverse range of state-of-the-art equipment and solutions, such as Vacuum Forming, Recycling Plastic, Sheet Film Line, Blow/Injection Molding Machines, EPE Foam Machines, Hydraulic Cutting Machines, and an array of auxiliary equipment like Air Compressors, Screw Compressors, Chillers, Hopper Dryers, Crushers, Mixers, and Auto Loaders. These products collectively form an intelligent integrated system that addresses material feeding, air supply, water supply, and power supply needs. Leveraging its technical expertise and robust supply chain, Champion is well-equipped to provide customized solutions to meet the specific demands of its customers.In line with its commitment to quality and reliability, Champion solidifies its reputation as a top manufacturer and supplier of plastic moulding machines. The company's state-of-the-art machines are designed to meet the diverse needs of small, medium, and large businesses across various industries. A combination of high-quality materials, cutting-edge technology, and stringent manufacturing processes ensures that Champion's machines deliver precision, efficiency, and durability.One of the company's key strategies for expanding its international reach is the focus on exploring new markets, particularly leveraging platforms like OLX to connect with potential customers looking for reliable plastic moulding machines. The company's products are now available on OLX, providing access to a wide range of customers and offering them high-quality machines at affordable prices.The plastic moulding machines offered by Champion are a testament to the company's dedication to innovation and high-quality manufacturing. The machines are suitable for a wide range of applications, including the production of toys, plastic containers, and more. Whether for large-scale manufacturing or small workshops, these machines are built to operate quickly and efficiently, enabling the production of a high volume of precision plastic moulds in a short time.Customer reviews of the Champion plastic moulding machines on OLX rave about their sleek design, intuitive interface, and ease of operation. Crafted from high-quality materials, the machines are built to withstand heavy use and produce high-quality molds consistently. Not only are they efficient, but they are also environmentally friendly, consuming less power than similar equipment on the market. Customers can rest assured in the knowledge that they have a reliable machine that streamlines their production process and produces consistent results.Champion's presence on OLX allows potential customers to access a wide variety of machines, compare different specifications, and benefit from an engaged community of users who can provide advice and recommendations. The company's commitment to offering competitive prices and exceptional customer support further enhances the value proposition for customers looking for a plastic moulding machine.In conclusion, Champion's dedication to quality, innovation, and international expansion has cemented its status as a top manufacturer and supplier of plastic moulding machines. With a global footprint and a presence on platforms like OLX, the company is well-positioned to connect with a wide range of customers and provide them with high-quality, reliable, and efficient plastic moulding machines that cater to their specific business needs.
Top Supplier of PVC Pipe Fitting Injection Molding Machines in China
and Injection Molding Machine.PVC Pipe Fitting Injection Molding Machine Supplier in ChinaInjection molding machines are widely used in various industries, including construction, automotive, packaging, and healthcare. Among the different types of injection molding machines, PVC pipe fitting injection molding machines are the most popular. These machines are specifically designed to manufacture PVC pipe fittings of various sizes and shapes with high precision.In China, there are several PVC pipe fitting injection molding machine suppliers, and one of the leading suppliers of these machines is (need remove brand name). The company has been manufacturing injection molding machines for over two decades and has gained a reputation for producing high-quality machines at competitive prices.The PVC pipe fitting injection molding machines manufactured by (need remove brand name) are designed to meet the specific requirements of the PVC pipe fitting industry. The machines are equipped with advanced technologies, including a closed-loop control system, which ensures high precision and consistency in every production cycle.Features of PVC Pipe Fitting Injection Molding MachineThe PVC pipe fitting injection molding machines manufactured by (need remove brand name) come with a range of advanced features that make them ideal for the production of high-quality PVC pipe fittings. Some of the key features of these machines include:1. High Precision: The machines are equipped with advanced technology, including a closed-loop control system, which ensures high precision in every production cycle. This ensures that the manufactured PVC pipe fittings are of high quality and meet industry standards.2. Energy-Efficient: The machines are designed to be energy-efficient, which helps in reducing the overall production cost. The machines are equipped with a special energy-saving system that reduces power consumption during operation.3. User-Friendly: The machines are designed to be user-friendly, which makes it easy for operators to operate and maintain. The machines come with a user-friendly interface and are easy to set up and configure.4. Customizable: The machines are customizable, which means that they can be tailored to meet the specific requirements of the PVC pipe fitting industry. The machines can be configured to produce pipe fittings of different sizes and shapes, depending on the needs of the customer.Benefits of Using PVC Pipe Fitting Injection Molding MachineThere are several benefits of using PVC pipe fitting injection molding machine for the production of pipe fittings. Some of the key benefits include:1. High Quality: The machines are designed to produce high-quality PVC pipe fittings that meet industry standards. The machines are equipped with advanced technology, which ensures high precision and consistency during the production cycle.2. Cost-Effective: The machines are designed to be cost-effective, which helps in reducing the overall production cost. The machines are energy-efficient, which reduces the cost of power consumption during operation.3. Fast Production: The machines are designed to produce PVC pipe fittings at a fast rate, which helps in meeting the growing demand for pipe fittings.4. Flexible: The machines are flexible and can be customized to meet the specific requirements of the PVC pipe fitting industry. The machines can produce pipe fittings of different sizes and shapes, depending on the needs of the customer.ConclusionIn conclusion, PVC pipe fitting injection molding machines are widely used in the PVC pipe fitting industry. In China, (need remove brand name) is one of the leading suppliers of these machines, and their machines are designed to meet the specific requirements of the PVC pipe fitting industry. The machines are equipped with advanced technology, which ensures high precision, consistency, and energy efficiency during the production cycle. The machines are cost-effective, flexible, and easy to operate and maintain, making them ideal for the production of high-quality PVC pipe fittings.
Manufacturer of Drip Irrigation Pipe Machine | Supplier and Factory of Drip Irrigation Tape Machinery
Champion Machinery is making significant strides in the global market with their innovative and high-quality products. With a focus on international expansion, the company has established a strong agent network across the globe and has been actively promoting and localizing the Champion brand. By engaging in face-to-face communication with customers, Champion has been able to enhance mutual understanding and improve service delivery to customers in various regions. The company's global footprint extends to Asia, Europe, Oceania, North and South America, Africa, and the Middle East, reflecting their commitment to serving customers worldwide.One of Champion Machinery's main product lines is their "many" Product System, consisting of six series of products that cater to different industrial needs. These include Vacuum Forming, Recycling plastic, Sheet film Line, Blow/Injection Molding Machine, EPE Foam Machine, and Hydraulic Cutting Machine. Additionally, the company offers a range of auxiliary equipment such as Air Compressors, Screw Compressors, Chillers, Hopper Dryers, Crushers, Mixers, and Auto Loaders. Champion's integrated system solutions provide intelligent, all-in-one solutions for Material Feeding, Air Supply, Water Supply, and Power Supply, demonstrating their technical expertise and supply chain advantages.In line with their commitment to global expansion, Champion Machinery has been focusing on providing solutions to international markets, including but not limited to the manufacturing of Drip Irrigation Pipe (Tape) Machines. These machines are designed to facilitate the production of high-quality drip irrigation systems, contributing to sustainability and cost-effectiveness in agriculture and horticulture. The innovative technology behind these machines ensures efficient water application and optimal growth for a wide range of crops, making them suitable for use in different soil compositions and crop types.Champion Machinery's Drip Irrigation Pipe Machine is built to high-quality standards, guaranteeing durability and reliability in the long run. The company's team of engineers and technical support personnel are committed to ensuring that the machines run smoothly and efficiently, using high-quality components to ensure longevity and performance. The precision of the Drip Irrigation Pipe Machine ensures uniform water application across fields or greenhouses, ultimately leading to substantial water and labor savings, and improved crop yields for farmers.In addition to their advanced machinery, Champion Machinery provides comprehensive support and services to their global customer base. By establishing a strong agent network and engaging in direct communication with customers, the company is able to understand and cater to the specific needs of each market, ensuring that their products meet the highest standards and expectations. With a commitment to constant improvement and innovation, Champion Machinery continues to be a leader in providing sustainable, cost-effective, and reliable solutions to the global market.As a result of their dedication to excellence and customer satisfaction, Champion Machinery has received rave reviews from satisfied customers across the globe. The Drip Irrigation Pipe Machine, in particular, has been hailed as an excellent investment for anyone looking to improve the efficiency and productivity of their irrigation systems. Customers have praised the machine for its ability to create high-quality drip irrigation pipes and tapes with speed and accuracy, allowing for efficient water application while conserving water in the process. The user-friendly interface and automatic control system make the machine suitable for both commercial and domestic use, while its durable construction ensures long-term performance and cost savings.Champion Machinery's commitment to providing top-quality machinery, combined with their dedication to customer service and global outreach, positions them as a formidable player in the international market. With an innovative product line and a strong focus on sustainability and customer satisfaction, Champion Machinery continues to lead the way in providing intelligent integrated system solutions for a wide range of industrial applications.
Understanding the Importance of Injection Speed in Injection Molding
Injection Speed In Injection MoldingInjection molding is a widely used manufacturing process for producing parts by injecting material into a mold. One of the crucial factors that determine the quality and efficiency of the process is the injection speed. Injection speed refers to the speed at which the material is injected into the mold. It plays a vital role in the overall production process, affecting the final product's quality, surface finish, and overall cycle time.Leading in the industry is {} (Company), a global leader in industrial manufacturing solutions. The company has a proven track record of providing high-quality injection molding machines and solutions to various industries worldwide.One of the key features of {}'s injection molding machines is their ability to control and adjust injection speed. This allows for a precise and efficient molding process, resulting in high-quality and consistent parts production.With the injection speed being a critical factor in the injection molding process, {} has developed state-of-the-art technology to ensure optimal performance. The company's injection molding machines are equipped with advanced control systems that allow operators to precisely adjust and monitor the injection speed, providing flexibility and control over the production process.Furthermore, {}'s injection molding machines are designed to achieve high injection speeds without compromising on the quality of the final product. This is achieved through innovative design and engineering, as well as the use of high-quality materials and components.The ability to adjust injection speed according to the specific requirements of each part and material is crucial in achieving the desired results. {}'s injection molding machines offer a wide range of injection speed options, allowing for versatility in production and ensuring that each part is manufactured with precision and accuracy.In addition to providing high-quality injection molding machines, {} also offers comprehensive support and solutions to its customers. The company's team of experts is dedicated to helping businesses optimize their production processes, providing guidance on injection speed optimization and other factors that can impact the overall efficiency and quality of production.{}'s commitment to innovation and excellence has made it a trusted partner for businesses looking to enhance their injection molding capabilities. With its advanced injection molding machines and expertise in injection speed control, {} continues to set the standard for quality and performance in the industry.In conclusion, injection speed is a critical factor in the injection molding process, and {} has proven itself as a leader in providing high-quality injection molding machines with advanced injection speed control capabilities. With its commitment to innovation and excellence, {} is a valuable partner for businesses looking to achieve optimal results in their injection molding operations.
Top Manufacturer and Supplier of Thread Cutting Machines - High-Quality Factory Direct Pricing
China-based Manufacturer leads the Market with Top-Quality Thread Cutting MachineIn the ever-evolving industrial landscape, the demand for precision machinery is at an all-time high. As industries continue to seek efficient and accurate solutions for their manufacturing processes, a reliable thread cutting machine has become essential. This is where the leading manufacturer and supplier of thread cutting machines, Champion, comes into play. Champion has established itself as a trusted OEM exporter and wholesale supplier of high-performance thread cutting machines, designed to meet the diverse needs of industrial applications.Champion's thread cutting machine is a high-performance precision tool that is built to provide efficiency and accuracy. With advanced features and state-of-the-art components, this machine guarantees optimal results, making it the go-to choice for industries with demanding requirements. The expert team of engineers at Champion has meticulously designed the machine to ensure that it meets and exceeds the expectations of their customers, setting it apart from the competition.What sets Champion's thread cutting machine apart is its sturdy and durable build, making it suitable for use in challenging industrial environments. The machine is easy to use and maintain, catering to the needs of both small and large-scale industrial operations. With the ability to cut threads quickly and accurately, Champion's machine ensures that production runs smoothly, saving time and contributing to overall operational efficiency.Champion's reputation as a top thread cutting machine manufacturer is further solidified by the company's commitment to high-quality materials and rigorous testing processes. These factors ensure that the machine is reliable and dependable, offering consistent performance over its operational lifespan. Customers can rely on Champion's thread cutting machine to deliver exceptional results, regardless of their industrial application.In addition to its precision and efficiency, the thread cutting machine from Champion provides a clean and precise cut every time. This ensures that industrial processes result in high-quality finished products, meeting the stringent standards of modern manufacturing. The machine comes with multiple cutting heads that can be easily adjusted to suit specific cutting requirements, offering versatility and adaptability to various manufacturing needs.Champion's dedication to customer satisfaction doesn't end with the quality of their machines. The company's global presence and commitment to localized service have made it a formidable force in the international market. With a well-established global agent network, Champion has worked tirelessly to promote and localize its brand, ensuring that customers worldwide have access to its top-quality products. Face-to-face communication with customers overseas has further improved mutual understanding and service, solidifying the company's reputation as a customer-focused organization.As a leading player in the market, Champion Machinery's main product system encompasses a wide range of offerings, including vacuum forming, recycling plastic, sheet film line, blow/injection molding machines, EPE foam machines, hydraulic cutting machines, air compressors, screw compressors, chillers, hopper dryers, crushers, mixers, and auto loaders. These intelligent integrated system solutions for material feeding, air supply, water supply, and power supply are a testament to Champion's technical strength and supply chain advantages, enabling the company to efficiently meet the customized demands of its customers.Customer testimonials further validate the quality and reliability of Champion's thread cutting machine. Users have praised the machine for its accuracy, speed, and ease of operation, making it a valuable addition to their industrial processes. Whether it's for fabric, ropes, cords, or any other material, Champion's thread cutting machine has consistently delivered on its promise of precision cutting, making it an indispensable tool for sewing and crafting projects alike.In conclusion, Champion's exemplary track record as a leading manufacturer, supplier, and exporter of high-quality thread cutting machines from China is a testament to the company's commitment to excellence. By delivering reliable, durable, and efficient machinery, Champion has set a new standard in the industry, providing unbeatable quality and reliability to its customers worldwide. With a focus on customer satisfaction, innovation, and precision, Champion continues to shape the future of industrial manufacturing with its cutting-edge solutions.