- Home
- Blog
- Top-Quality Injection Moulding Dryers and Hopper Dryers to meet Diverse Material Needs in UK
Top-Quality Injection Moulding Dryers and Hopper Dryers to meet Diverse Material Needs in UK
By:admin
Shini is a leading manufacturer of drying and dehumidifying solutions for the plastics industry, providing a wide range of products to cover different material characteristics and throughputs. Its line of hopper dryers is designed to maintain consistent and uniform drying of plastic materials, providing high-quality results every time.
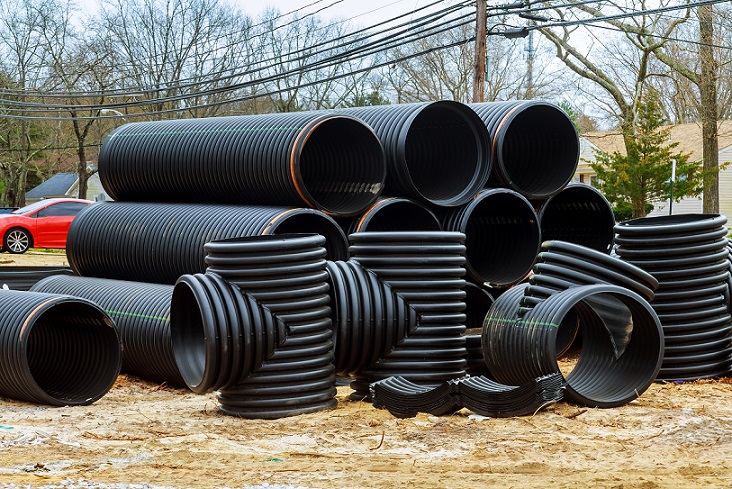
Shini hopper dryers come with a host of features that promote efficiency and reliability. For instance, they have a stainless steel hopper that ensures there is no contamination of the material during the drying process. The hopper is also insulated to conserve energy and minimize heat loss.
Another feature that sets Shini hopper dryers apart is the digital microprocessor control system. This feature provides accurate and precise control over the drying process, allowing for customization to match different materials. Additionally, the system comes with alarms and safety features that ensure safe operation and protection against over-heating or over-drying.
Shini hopper dryers also come with an air distribution system that ensures the uniform distribution of hot air within the hopper. The system's design allows for efficient heat transfer, ensuring that the drying process is quick and effective. This is especially important when dealing with moisture-sensitive materials that require quick and thorough drying.
In terms of capacity, Shini hopper dryers come in different sizes to match varying throughputs. This means that manufacturers can choose the right hopper dryer for their production needs, without having to worry about under or over-drying materials.
When it comes to maintenance, Shini hopper dryers are designed with ease of use in mind. The modular construction allows for easy cleaning and servicing of components, reducing downtime and maintenance costs.
In conclusion, Shini is a name that is synonymous with high-quality and reliable drying and dehumidifying solutions. Its line of hopper dryers is no exception, providing manufacturers with the tools they need to ensure consistent and uniform drying of plastic materials. If you are looking for a hopper dryer that combines efficiency, reliability, and ease of use, look no further than Shini Hopper Dryer.
Company News & Blog
High-Quality Pet PP PS PE ABS Sheet Extrusion Production Line: Latest News
Title: Leading Manufacturer Announces Advanced Pet Pp Ps Pe Abs Sheet Extrusion Production LineIntroduction:As the demand for high-quality plastic products continues to grow, leading manufacturer {Company Name} is proud to announce the launch of their state-of-the-art Pet Pp Ps Pe Abs Sheet Extrusion Production Line. This innovative technology aims to revolutionize the industry by providing efficient and eco-friendly solutions to meet the ever-evolving needs of various sectors that rely on plastic sheets for their operations.Enhanced Production Capabilities:The new Pet Pp Ps Pe Abs Sheet Extrusion Production Line offers enhanced production capabilities, enabling {Company Name} to meet the increasing demand for plastic sheet products. This cutting-edge production line utilizes advanced extrusion techniques to create superior quality sheets with heightened precision and consistency.Eco-Friendly Design:In recognition of the need for sustainable manufacturing practices, {Company Name} has ensured that their Pet Pp Ps Pe Abs Sheet Extrusion Production Line incorporates eco-friendly features. The latest technology includes energy-efficient mechanisms and recycling systems that minimize waste and reduce environmental impact. By focusing on sustainability, {Company Name} aims to contribute to a greener and more responsible future.Superior Quality and Versatility:The Pet Pp Ps Pe Abs Sheet Extrusion Production Line by {Company Name} is engineered to deliver superior quality sheets that can be customized to suit a wide range of applications. These sheets exhibit excellent mechanical properties, exceptional durability, and resistance to chemicals, making them ideal for diverse industries such as packaging, automotive, construction, and more.Automated Monitoring and Control System:To ensure flawless production processes and consistent product quality, {Company Name}'s Pet Pp Ps Pe Abs Sheet Extrusion Production Line is equipped with an automated monitoring and control system. This state-of-the-art system continuously monitors key parameters, such as temperature, speed, and pressure, to guarantee optimal operating conditions. Any deviations are promptly identified, minimizing product defects and ensuring customer satisfaction.Collaborative Approach:In line with their commitment to forging strong relationships with customers, {Company Name} emphasizes a collaborative approach. By working closely with clients, they can understand specific requirements and develop tailored solutions using the Pet Pp Ps Pe Abs Sheet Extrusion Production Line. This customer-centric approach ensures that the final products meet or exceed industry standards and expectations.Commitment to R&D and Innovation:{Company Name} is renowned for its dedication to research and development, constantly striving to remain at the forefront of technological advancements in the plastic extrusion industry. With their Pet Pp Ps Pe Abs Sheet Extrusion Production Line, they have once again demonstrated their commitment to innovation. Through continuous improvements and new developments, {Company Name} aims to offer cutting-edge solutions that cater to evolving market needs.Conclusion:The introduction of {Company Name}'s advanced Pet Pp Ps Pe Abs Sheet Extrusion Production Line marks a significant milestone in the plastic extrusion industry. Utilizing state-of-the-art technology, eco-friendly features, and a collaborative approach, {Company Name} is set to deliver high-quality plastic sheets that meet various industry requirements. As they continue to invest in research and development, {Company Name} positions itself as a leading manufacturer, providing innovative solutions for a sustainable future.
Buy High-Quality Plastic Moulding Machine on OLX - Wholesale Deals from China
Champion, a leading manufacturer and supplier of plastic moulding machines based in China, is making waves in the international market with its commitment to quality and innovation. With a strong focus on global expansion, Champion has established a robust network of agents around the world and actively promoted its brand on a localized level.The company has been actively seeking out new opportunities in international markets, and its efforts have paid off as its footprints have extended to Asia, Europe, Oceania, North and South America, Africa, and the Middle East. This global presence has allowed Champion to engage in face-to-face communication with customers overseas, ultimately leading to improved mutual understanding and enhanced service delivery.Champion's main product lineup includes a diverse range of state-of-the-art equipment and solutions, such as Vacuum Forming, Recycling Plastic, Sheet Film Line, Blow/Injection Molding Machines, EPE Foam Machines, Hydraulic Cutting Machines, and an array of auxiliary equipment like Air Compressors, Screw Compressors, Chillers, Hopper Dryers, Crushers, Mixers, and Auto Loaders. These products collectively form an intelligent integrated system that addresses material feeding, air supply, water supply, and power supply needs. Leveraging its technical expertise and robust supply chain, Champion is well-equipped to provide customized solutions to meet the specific demands of its customers.In line with its commitment to quality and reliability, Champion solidifies its reputation as a top manufacturer and supplier of plastic moulding machines. The company's state-of-the-art machines are designed to meet the diverse needs of small, medium, and large businesses across various industries. A combination of high-quality materials, cutting-edge technology, and stringent manufacturing processes ensures that Champion's machines deliver precision, efficiency, and durability.One of the company's key strategies for expanding its international reach is the focus on exploring new markets, particularly leveraging platforms like OLX to connect with potential customers looking for reliable plastic moulding machines. The company's products are now available on OLX, providing access to a wide range of customers and offering them high-quality machines at affordable prices.The plastic moulding machines offered by Champion are a testament to the company's dedication to innovation and high-quality manufacturing. The machines are suitable for a wide range of applications, including the production of toys, plastic containers, and more. Whether for large-scale manufacturing or small workshops, these machines are built to operate quickly and efficiently, enabling the production of a high volume of precision plastic moulds in a short time.Customer reviews of the Champion plastic moulding machines on OLX rave about their sleek design, intuitive interface, and ease of operation. Crafted from high-quality materials, the machines are built to withstand heavy use and produce high-quality molds consistently. Not only are they efficient, but they are also environmentally friendly, consuming less power than similar equipment on the market. Customers can rest assured in the knowledge that they have a reliable machine that streamlines their production process and produces consistent results.Champion's presence on OLX allows potential customers to access a wide variety of machines, compare different specifications, and benefit from an engaged community of users who can provide advice and recommendations. The company's commitment to offering competitive prices and exceptional customer support further enhances the value proposition for customers looking for a plastic moulding machine.In conclusion, Champion's dedication to quality, innovation, and international expansion has cemented its status as a top manufacturer and supplier of plastic moulding machines. With a global footprint and a presence on platforms like OLX, the company is well-positioned to connect with a wide range of customers and provide them with high-quality, reliable, and efficient plastic moulding machines that cater to their specific business needs.
China Manufacturer of Injection Stretch Blow Molding Machine - Your Trusted Supplier and Factory" --> "Injection Stretch Blow Molding Machine - Reliable China-based Manufacturer, Supplier, and Factory
Champion Machinery, a leading manufacturer and supplier of injection stretch blow molding machines, is making waves in the global market with its high-quality products and efficient packaging solutions. The company has been dedicated to exploring international markets and establishing a strong agent network around the world. With a wide range of products including Vacuum forming, Recycling plastic, Sheet film Line, Blow/injection molding machine, EPE foam machine, Hydraulic cutting machine, Air compressor/Screw compressor/Chiller/Hopper dryer/Crusher/Mixer/Auto loader all in 1 intelligent integrated system solutions for Material Feeding, Air Supply, Water Supply and Power Supply, Champion Machinery is well-equipped to meet the diverse needs of customers worldwide.The Injection Stretch Blow Molding Machine offered by Champion Machinery is a highly-efficient and advanced manufacturing machine that is widely used in the production of plastic bottles and containers for various industries. The company's commitment to providing top-of-the-line manufacturing solutions ensures that the Injection Stretch Blow Molding Machine is designed with state-of-the-art technology – enabling it to produce high-quality plastic products with precision, speed, and efficiency.Designed with a user-friendly interface, the Injection Stretch Blow Molding Machine is easy to operate, even for those with minimal technical skills. Its advanced features, including a high-speed servo system, auto-deflashing system, and advanced temperature control, make it the perfect solution for businesses looking to produce top-quality plastic bottles. The machine's intelligent design ensures maximum reliability, and its easy-to-use interface makes it accessible to anyone.The injection stretch blow molding technology allows manufacturers to produce high-quality, complex plastic containers with great precision and speed. By combining injection molding and blow molding techniques, the machine can produce finished products that are lightweight, visually appealing, and highly resistant to breakage. It offers a cost-effective and efficient way to meet the needs of a wide range of industries, providing manufacturers with the ability to create containers in a variety of shapes and sizes, with different finishes and textures.The machine can be used to produce bottles and containers for food and beverages, cosmetics and personal care products, as well as industrial chemicals and lubricants. It is also suitable for producing specialized products like medical devices and automotive parts. With its high level of precision and control, the Injection Stretch Blow Molding Machine is an essential piece of equipment for manufacturers who want to produce high-quality, customized plastic containers.Champion Machinery's global reach has allowed the company to make a significant impact on the international market. With footprints all over the world, including Asia, Europe, Oceania, North and South America, Africa, and the Middle East, Champion Machinery has demonstrated its commitment to providing efficient and reliable solutions to customers worldwide.The company's focus on customer service is evident in its efforts to pay visits to customers overseas for face-to-face communication, which helps to improve mutual understanding and service to customers. This dedication to building strong relationships with customers has contributed to Champion Machinery's success in the global market.In conclusion, Champion Machinery's Injection Stretch Blow Molding Machine offers exceptional performance and versatility for producing high-quality plastic bottles and containers. The company's global strategy and dedication to exploring international markets have positioned it as a reliable, durable, and cost-efficient option for businesses in the plastic manufacturing industry. With its technical strength and supply chain advantages, Champion Machinery is well-equipped to meet the customized demand for material feeding, air supply, water supply, and power supply, providing efficient and intelligent integrated system solutions to customers worldwide.
Plastic Compression Machines - Reliable Supplier and Factory Direct from China
Champion Machinery, a leading manufacturer and supplier in the field of plastic processing equipment, has been making significant strides in the global market with their high-quality products and innovative solutions. With a strong focus on international expansion, Champion Machinery has successfully established a global agent network and promoted their brand to meet the diverse needs of customers worldwide.The company's commitment to excellence and customer satisfaction has led to their presence in various regions, including Asia, Europe, Oceania, North and South America, Africa, and the Middle East. Champion Machinery has prioritized face-to-face communication with their international customers, which has not only improved mutual understanding but also enhanced the level of service provided to their clients.Champion Machinery's main product system includes a wide range of products such as Vacuum Forming, Recycling Plastic, Sheet Film Line, Blow/Injection Molding Machine, EPE Foam Machine, Hydraulic Cutting Machine, Air Compressor/Screw Compressor, Chiller, Hopper Dryer, Crusher, Mixer, and Auto Loader. These products are part of an intelligent integrated system solution for material feeding, air supply, water supply, and power supply, providing efficient and customizable solutions based on the company's technical strength and supply chain advantages.In line with their dedication to delivering top-quality products, Champion Machinery has further expanded their offerings to include the highly sought-after Plastic Compression Machine. This essential piece of equipment is designed to compress and shape raw plastic materials into specific forms, allowing for further processing to create a variety of products. The machine operates by applying heat and pressure to the plastic materials, resulting in a compact mass that meets the highest standards of quality and consistency.Champion Machinery's Plastic Compression Machine is built with the latest technology and innovation, ensuring optimal performance and quality output. The machines are made from high-grade materials, providing durability and long-lasting use even under tough working conditions and heavy usage. With a wide range of options available, these machines are suitable for various applications such as molding, extrusion, and shaping, making them ideal for producing high-quality products in a cost-effective manner.Customers who have utilized Champion Machinery's Plastic Compression Machine have praised its advanced technology and modern features, as well as its ease of use and maintenance. The machine's high-pressure capacity ensures the complete compression of plastic materials, making it a top-quality product that significantly boosts the production capacity and quality of any plastic manufacturing business.Furthermore, the Plastic Compression Machine has been recognized as an essential tool for businesses dealing with plastic manufacturing, helping them create durable and reliable products consistently. Its easy-to-use interface and precise control features make plastic compression effortless, while its outstanding build quality ensures functionality for years with minimal maintenance. This makes the machine an excellent investment for businesses looking to produce high-quality and environmentally friendly plastic products and improve their production processes while reducing overhead costs.With their unwavering dedication to technological innovation and superior customer service, Champion Machinery continues to be a leading force in the global market for plastic processing equipment. Their commitment to providing top-quality products and solutions has set them apart as a preferred choice for businesses around the world.For businesses looking to increase productivity and profitability, Champion Machinery's Plastic Compression Machine is a smart choice that aligns with their mission to deliver efficient and reliable solutions to the plastic processing industry. With a proven track record of excellence and a commitment to meeting the evolving needs of customers, Champion Machinery is poised to remain a trusted partner for businesses seeking to stay competitive in the fast-paced world of manufacturing.
High-Quality Plastic Chips Machine Manufacturer, Supplier, and Factory in China
Plastic Chips Machine Revolutionizing Plastic Processing Industry"The global plastic processing industry has been revolutionized by the introduction of high-quality Plastic Chips Machine from a renowned company in China. This leading Manufacturer, Supplier, and Factory has taken pride in offering top-of-the-line plastic processing equipment that is efficient, reliable, and eco-friendly. With advanced technology and precision engineering, their Plastic Chips Machine is designed to produce high-quality plastic chips from a variety of materials, including PE, PP, and PS.The machine is specifically designed to grind and process plastic materials into small granules, making it easier to recycle and repurpose. It is perfect for processing plastic waste from various industries such as packaging, construction, and manufacturing. Equipped with high-quality cutting blades and a powerful motor, the Plastic Chips Machine can process a wide range of plastic materials including PET, HDPE, LDPE, PVC, and more. It is also designed for easy cleaning and maintenance, ensuring a long-lasting and trouble-free operation.The company's commitment to providing the highest level of customer service and technical support has set them apart in the industry. Their expert team is readily available to answer any questions and provide assistance to ensure smooth operations and optimal performance of the Plastic Chips Machine.The impact of the Plastic Chips Machine goes beyond just efficiency and productivity. By transforming plastic waste into granules, the company is actively contributing to reducing the amount of plastic waste that ends up in landfills and oceans. Investing in this machine is not only a practical way to improve business operations but also a meaningful step towards promoting sustainability and reducing carbon footprint.Customers who have invested in the Plastic Chips Machine have been highly satisfied with its performance and impact on their businesses. Ms. Carlen Shu, a business owner who produces large quantities of plastic chips, expressed that the machine has saved countless hours of manual labor and frustration. Its efficiency, high-quality output, and minimal maintenance make it a great investment for any business looking to increase productivity and profitability.Ms. Angela Her, another customer, emphasized that investing in a Plastic Chips Machine is a practical way to reduce carbon footprint, promote sustainability, and generate additional income. She highlighted the easy use, minimal maintenance, and high-quality end product as key benefits of this machine for businesses that utilize plastic materials.The global reach of the company has been expanding rapidly, with an established agent network and footprints all around the world including Asia, Europe, Oceania, North and South America, Africa, and the Middle East. Their dedication to face-to-face communication with customers overseas has improved mutual understanding and service, further enhancing their global presence and impact in the industry.Champion machinery's main products, including Vacuum forming, Recycling plastic, Sheet film Line, Blow/injection molding machine, EPE foam machine, and Hydraulic cutting machine, are part of the extensive Product System. This system provides intelligent integrated solutions for Material Feeding, Air Supply, Water Supply, and Power Supply, efficiently meeting customized demand based on technical strength and supply chain advantages.The company's commitment to innovation, quality, and sustainability has positioned them as a leader in the plastic processing industry. The introduction of the Plastic Chips Machine has not only transformed businesses but also contributed to reducing plastic waste and promoting environmental responsibility. As they continue to expand their global presence, their impact on the industry and the environment is set to grow even further. For businesses looking to improve their plastic processing operations and make a positive impact on the environment, investing in the Plastic Chips Machine from this leading company in China is a step in the right direction.
Top Injection Molding Manufacturer and Supplier in China - Factory Prices
Champion machinery, a leading manufacturer and supplier of injection molding machines and other plastic processing equipment, is making significant strides in the global market. As the company continues to expand its international presence, it has focused on building a strong network of agents and promoting its brand in various regions around the world.With a dedicated effort to explore new markets, Champion has established a global agent network that has been growing steadily. By actively engaging with customers in different countries, the company has been able to enhance its understanding of their specific needs and provide tailored solutions. Champion's commitment to face-to-face communication has played a crucial role in strengthening relationships with clients around the globe.One of Champion's core product offerings is the "many" Product System, which comprises a diverse range of equipment, including vacuum forming, recycling plastic, sheet film lines, blow/injection molding machines, EPE foam machines, hydraulic cutting machines, and various auxiliary equipment such as air compressors, screw compressors, chillers, hopper dryers, crushers, mixers, and auto loaders. These products are part of an intelligent integrated system that provides solutions for material feeding, air supply, water supply, and power supply, catering to the diverse needs of the plastic processing industry.Champion's technical expertise and robust supply chain enable the company to efficiently meet customized demands from clients. With a strong focus on innovation and quality, Champion machinery is well-positioned to deliver high-performance solutions to its global customer base.In addition to its product offerings, Champion is particularly known for its injection molding machines, which are designed to meet the demanding requirements of modern manufacturing. With a commitment to precision, reliability, and efficiency, Champion's injection molding machines have proven to be invaluable assets for a wide range of production applications.While Champion continues to expand its footprint globally, its core values of quality, reliability, and customer satisfaction remain unwavering. By prioritizing customer service and product excellence, Champion is poised to make a lasting impact in the international market.The company's efforts have not gone unnoticed, as it has garnered positive reviews from customers worldwide. With advanced technology, high precision, and optimal efficiency, Champion's injection molding machines have received acclaim for their exceptional performance and cost-effectiveness. Customers have highlighted the user-friendly nature of the machines, as well as their capability to handle a wide range of materials while delivering excellent quality finished products.As Champion continues to solidify its presence in Asia, Europe, Oceania, North and South America, Africa, and the Middle East, the company is well-positioned to become a leading global player in the plastic processing industry. With a strong focus on international expansion and a commitment to meeting the unique needs of customers in diverse markets, Champion machinery is poised for continued success on the global stage.
Revolutionary Desktop Injection Molding Machine - Unlocking Affordable Manufacturing at Home
Title: Game-Changing Desktop Plastic Injection Machines Revolutionize Small-Scale ManufacturingIntroduction:In today's fast-paced world, innovation is the key to success. One such groundbreaking innovation is the emerging market of desktop plastic injection machines. These compact devices are paving the way for small-scale manufacturers to accelerate production, reduce costs, and level the playing field with larger competitors. One prominent player in this industry is __________, a leading manufacturer of advanced desktop plastic injection machines. With cutting-edge technology and a reputation for excellence, __________ is transforming the way small businesses approach manufacturing.Body:1. The Rise of Desktop Plastic Injection MachinesDesktop plastic injection machines are reshaping the manufacturing landscape by enabling businesses to produce high-quality plastic parts in-house. Previously, manufacturers had to rely on expensive, large-scale injection molding machines, making small production runs financially impractical. However, with the technological advancements made by companies like __________, small-scale manufacturers can now access affordable and efficient plastic injection machines right at their fingertips.2. __________: Revolutionizing the Industry__________, a renowned company specializing in desktop plastic injection machines, is at the forefront of this revolution. With its state-of-the-art machines and commitment to customer satisfaction, __________ has rapidly gained recognition as an industry leader. Their machines uphold the highest quality standards while providing ease of use, cost-effectiveness, and the ability to create complex parts with precision.3. Advantages of Desktop Plastic Injection MachinesThese modern devices offer several advantages over traditional injection molding machines. Firstly, their compact size allows them to be used in small workshop settings, accommodating businesses with limited space. Additionally, desktop plastic injection machines require significantly less energy consumption, making them environmentally friendly and reducing operational costs. By eliminating the need for third-party manufacturers, these machines enable businesses to retain control over their production process and maintain confidentiality of their designs.4. Democratising ManufacturingPrior to the advent of desktop plastic injection machines, small-scale manufacturers often faced challenges accessing the same level of production capabilities as their larger counterparts. These machines have revolutionized the field, democratizing manufacturing and enabling entrepreneurs and startups to compete effectively. The shift from outsourcing to in-house production empowers businesses to be more agile, responsive, and adaptable to market demands.5. Applications Across IndustriesDesktop plastic injection machines have a wide range of applications, making them relevant across various industries. From automotive components to consumer electronics, medical devices to consumer goods, these machines can cater to diverse production needs. With customization options available, businesses can tailor their production with precision to meet specific product requirements.6. Ease of Use and AutomationOne of the key attributes of __________'s desktop plastic injection machines is their user-friendly interface, making them accessible even to those without extensive technical knowledge. These machines are designed to simplify the injection molding process, allowing manufacturers to automate certain repetitive tasks, thereby optimizing production efficiency and reducing human error. The intuitive software and advanced control systems provide real-time data feedback for seamless and precise molding operations.7. Quality Assurance and Cost ReductionQuality control plays a crucial role in the manufacturing process. Desktop plastic injection machines, including those offered by __________, incorporate advanced sensors and monitoring systems to ensure consistency and accuracy in product output. By eliminating the need for outsourcing, businesses can cut costs significantly, reduce lead times, and improve quality control, contributing to better overall customer satisfaction.Conclusion:Desktop plastic injection machines are revolutionizing small-scale manufacturing by providing businesses with the tools they need to compete effectively in the market. Companies like __________ are spearheading this paradigm shift, offering cutting-edge technology, user-friendly interfaces, and cost-effective solutions. As the adoption of these machines increases, we can expect to witness a transformation in the manufacturing landscape, driving innovation, enhancing productivity, and transforming the way businesses operate.
Addressing Pollution: The Solution Lies in Biodegradable Plastics
Title: Biodegradable Plastic: The Ultimate Solution to Curb PollutionIntroductionEarth, our only home, is currently facing a serious threat to its life-supporting ability due to the alarming increase in pollution caused by human activities. Among the numerous factors contributing to this decline, the introduction of harmful substances into the environment and their subsequent impact on the ecosystem is a major concern. One such harmful substance is plastic, which has become a persistent problem worldwide. However, there is a potential solution that holds great promise in tackling this issue head-on: biodegradable plastic. In this blog post, we will explore the significance of biodegradable bags and the manufacturing machines that are revolutionizing the plastic industry.Understanding the Plastic Pollution CrisisPlastic has undoubtedly revolutionized various industries, offering convenience and versatility. However, the improper disposal and inadequate recycling of conventional plastic have resulted in a catastrophic environmental crisis. Traditional plastic takes hundreds of years to decompose, leading to the accumulation of plastic waste in landfills, water bodies, and even in the most remote corners of our planet. This not only harms wildlife and marine life but also poses a grave threat to human health.Biodegradable Plastic: A Sustainable AlternativeThe introduction of biodegradable plastic has emerged as a game-changer in the fight against plastic pollution. Unlike conventional plastic, biodegradable plastic has the unique ability to break down and decompose into natural elements over a relatively short period. This means that it does not leave lasting negative impacts on the environment. Biodegradable bags, made from this innovative material, are attracting global attention as a sustainable substitute for single-use plastic bags.Why Biodegradable Bags MatterBiodegradable bags offer a range of benefits when compared to traditional plastic bags. Firstly, they significantly reduce the burden on landfills and waste management systems, as they decompose effectively. Secondly, they do not contribute to the ever-growing plastic pollution crisis. Thirdly, the production process for biodegradable bags has a lower carbon footprint, making them more eco-friendly. Fourthly, these bags possess the same strength and durability as their conventional counterparts, ensuring that they can still serve their intended purpose without compromising on quality.The Role of Biodegradable Bag Manufacturing MachinesThe rapid shift towards biodegradable bags requires an efficient and cost-effective manufacturing process. This has led to the development of advanced biodegradable bag manufacturing machines. These machines utilize cutting-edge technology to produce high-quality biodegradable bags in large quantities. With precise control over parameters such as size, thickness, and material composition, manufacturers can cater to diverse industrial and consumer needs.Keywords: Biodegradable Bags Manufacturing MachineTo ensure optimal visibility in search engine results, it is crucial to incorporate relevant keywords into the content. The focus keyword for this article, "Biodegradable Bags Manufacturing Machine," helps target readers actively seeking information on this specific topic. By naturally including this keyword throughout the blog post, we can enhance its relevance and visibility on search engines, thus boosting its search engine optimization (SEO) potential.ConclusionThe plastic pollution crisis is a global concern that demands immediate action. Biodegradable plastic, particularly in the form of biodegradable bags, offers a viable solution to curbing pollution and preserving our planet for future generations. As awareness grows and technology advances, incorporating biodegradable bags manufacturing machines into industry practices will help accelerate the transition towards a sustainable future. By embracing this eco-friendly alternative, we can pave the way for a cleaner, greener, and healthier planet Earth.
Wholesale Pet Series of Single Screw Extrusion Sheet Line from Manufacturer in China
Champion Machinery, a leading manufacturer of plastic extrusion equipment, has reached new heights in its global strategy, with a strong focus on exploring international markets. The company has been actively establishing a global agent network and promoting the Champion brand in various regions. With a presence in Asia, Europe, Oceania, North and South America, Africa, and the Middle East, Champion Machinery has made significant strides in expanding its international footprint.The company's commitment to customer service is evident in its approach to face-to-face communication with customers overseas. This personalized approach has helped improve mutual understanding and strengthen the company's service to its customers. By aligning its efforts with the needs of international markets, Champion Machinery has demonstrated its dedication to providing top-quality products and services across the globe.One of Champion Machinery's main products is the "Pet Series of Single Screw Extrusion Sheet Line," a revolutionary product that has redefined pet sheet extrusion. This state-of-the-art product is designed to provide superior quality and efficiency for pet sheet production. With a focus on producing high-quality pet sheets with a variety of thicknesses, widths, and finishes, the Pet Series has become an essential tool for businesses looking to create top-notch pet products that stand the test of time.The Pet Series of Single Screw Extrusion Sheet Line is a versatile and user-friendly product that offers advanced features and a cutting-edge design. The extrusion process is fully automated, ensuring consistency in sheet thickness and quality. Moreover, the line is equipped with advanced control systems that allow for precise control of production speed, temperature, and pressure. This level of precision and automation sets the Pet Series apart as an industry-leading solution for pet sheet production.The product line's environmental impact is also noteworthy, as it enables the production of thinner sheets, reducing waste and minimizing the carbon footprint. This emphasis on sustainability aligns with Champion Machinery's commitment to responsible manufacturing practices and environmental stewardship.Customer reviews of the Pet Series of Single Screw Extrusion Sheet Line highlight the product's exceptional quality, durability, and ease of operation. Customers praise the machine for its ability to create high-quality and durable sheets, suitable for various pet product applications. The streamlined design of the machine makes cleaning and maintenance a breeze, while its user-friendly interface ensures efficient operation and production of different thicknesses and sizes.In addition to the Pet Series, Champion Machinery offers a comprehensive range of products, including Vacuum forming, Recycling plastic, Sheet film Line, Blow/injection molding machine, EPE foam machine, Hydraulic cutting machine, as well as integrated system solutions for material feeding, air supply, water supply, and power supply. These products are designed to meet the customized demands of customers, leveraging the company's technical strength and supply chain advantages.As a trusted and reputable manufacturer, supplier, and factory of plastic extrusion equipment, Champion Machinery continues to lead the industry with innovative products and exceptional customer service. The company's dedication to excellence and commitment to meeting the highest quality standards make it a preferred choice for businesses seeking reliable and efficient extrusion equipment.In conclusion, Champion Machinery's expansion into international markets and its commitment to delivering top-quality products, such as the Pet Series of Single Screw Extrusion Sheet Line, reinforce the company's position as a global leader in the plastic extrusion industry. With a focus on innovation, sustainability, and customer satisfaction, Champion Machinery remains at the forefront of shaping the future of plastic extrusion technology.
Discover the Innovative TJS-670 Double Layer PP/PS Sheet Extruder for your Production Needs
Title: Discover the Powerful Pp/Ps Double Layer Sheet Extruder: Enhancing Your Manufacturing ProcessIntroduction:Welcome to our blog, where we explore the revolutionary TJS-670 double layer PP/PS sheet extruder. In this article, we will delve into the various features and benefits of this machinery, shedding light on how it can optimize your manufacturing process. Let's dive in!1. Understanding the TJS-670 Double Layer PP/PS Sheet Extruder:The TJS-670 double layer PP/PS sheet extruder is the latest innovation in the world of plastic sheet extrusion. Developed by Rui'an Litai Machinery CO.,LTD, this machine boasts top-notch technology, ensuring high-speed and efficient production of double-layer polypropylene (PP) and polystyrene (PS) sheets. With its seamless functionality and flexible adjustments, this extruder is designed to meet the diverse needs of plastic sheet manufacturers.2. Efficient Production Techniques:The TJS-670 double layer PP/PS sheet extruder excels in enabling high-speed production while maintaining excellent sheet quality. Equipped with advanced heating systems and precise temperature control, this machinery ensures uniform heat distribution throughout the extrusion process. This leads to consistent product quality, minimized defects, and reduced waste, ultimately enhancing overall efficiency.3. Dual-Layer Extrusion Capabilities:One of the key features of the TJS-670 extruder is its ability to produce double-layer sheets. By utilizing specialized technology, this machine facilitates the extrusion of two layers simultaneously, resulting in enhanced functionality and durability of the manufactured sheets. This feature opens up a plethora of possibilities for manufacturers looking to provide their customers with premium quality double-layer PP/PS sheets.4. Versatile Application and Customization:The TJS-670 double layer PP/PS sheet extruder enables manufacturers to produce sheets of varying thicknesses, ranging from 0.3mm to 2mm. Moreover, it offers great flexibility in terms of sheet width, with a range of 600mm to 1600mm. This versatility allows manufacturers to cater to diverse industry requirements, whether it be for packaging, stationery, signage, or other applications.5. User-Friendly Controls and Safety Measures:Rui'an Litai Machinery CO.,LTD has prioritized user convenience and safety in the design of the TJS-670 double layer PP/PS sheet extruder. The machine is equipped with an easy-to-use touch screen control panel, allowing operators to monitor and adjust various parameters with precision. Furthermore, built-in safety features ensure the protection of operators during the production process, making it a reliable and secure choice for manufacturers.Conclusion:In conclusion, the TJS-670 double layer PP/PS sheet extruder manufactured by Rui'an Litai Machinery CO.,LTD is a game-changer for plastic sheet manufacturers. By streamlining production, offering dual-layer capabilities, and ensuring versatility and user-friendly controls, this innovative machine provides manufacturers with an edge in the market. Embrace this cutting-edge technology and elevate your manufacturing process to new heights.Keywords: PP/PS double layer sheet extruder, TJS-670 extruder, Rui'an Litai Machinery CO.,LTD, plastic sheet manufacturing, high-speed production, sheet quality, dual-layer extrusion, versatile application, customization, user-friendly controls, safety measures.