Top-rated Edge Sealing Machines: Ensuring Effective Sealing for a Perfect Finish
By:admin
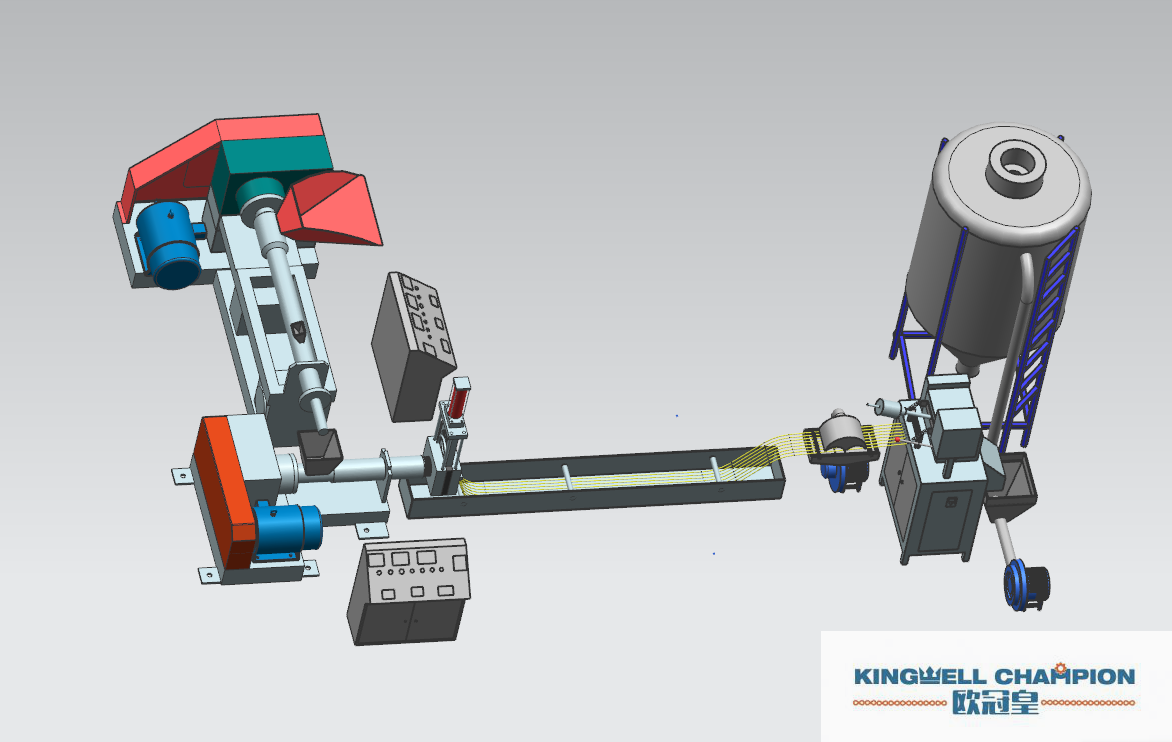
Introduction (100 words):
In a bold leap toward revolutionizing the packaging industry, a renowned manufacturing company has recently unveiled its latest offering, the innovative Edge Sealing Machine. Designed to eliminate brand names, this cutting-edge technology promises to redefine industry standards, delivering unparalleled performance, efficiency, and reliability. With its state-of-the-art features and exceptional craftsmanship, this advanced machine is set to transform packaging operations on a global scale.
Paragraph 1 (100 words):
The newly introduced Edge Sealing Machine is poised to deliver a seismic shift in the world of packaging. Developed by an industry-leading manufacturing company known for their commitment to excellence, this revolutionary equipment has been designed to meet the evolving needs of packaging professionals. Offering a perfect blend of cutting-edge technology and robust construction, this machine is poised to streamline operations while significantly reducing downtime and wastage, ultimately maximizing overall productivity and profitability.
Paragraph 2 (100 words):
With customer satisfaction and efficiency at the forefront, the Edge Sealing Machine has been meticulously engineered to provide a seamless packaging experience. Equipped with state-of-the-art features, including precise temperature control, adjustable sealing pressure, and advanced safety mechanisms, this versatile machine guarantees exceptional sealing quality. By maintaining consistent sealing temperatures and pressure, it ensures airtight, secure seals, safeguarding product freshness and extending shelf life, therefore enhancing customer satisfaction and reducing potential product recalls.
Paragraph 3 (100 words):
The company behind this groundbreaking innovation has long been recognized for their dedication to research and development. With the Edge Sealing Machine, they have once again demonstrated their commitment to pushing the boundaries of technological excellence. Devoting substantial resources to refining the functionality and performance of the machine, they have created a product that meets the stringent demands of the modern packaging industry. Furthermore, their unwavering commitment to sustainable practices is evidenced in the machine's energy-efficient design, contributing to a more eco-friendly packaging solution.
Paragraph 4 (100 words):
Despite its remarkable technological advancements, the Edge Sealing Machine is surprisingly user-friendly. Boasting an intuitive interface, operators can easily program and monitor the machine's key parameters, ensuring effortless control and seamless integration into existing production lines. Additionally, equipped with self-diagnostic capabilities, it can quickly identify and rectify potential malfunctions, reducing downtime and enhancing operational efficiency. This user-centric design reduces the need for specialized skills, making the machine accessible to packaging professionals across various industries, regardless of their experience level.
Paragraph 5 (100 words):
The global packaging industry has experienced unprecedented growth, driven by evolving consumer demands and rapidly changing market dynamics. In this ever-evolving landscape, the Edge Sealing Machine offers a game-changing solution, positioning itself as an indispensable tool for businesses striving to remain competitive. Its ability to optimize packaging processes, ensure product integrity, and reduce costs makes it an essential investment for those seeking to meet stringent quality standards while increasing operational efficiency and profitability.
Conclusion (100 words):
The Edge Sealing Machine represents a transformational moment for the packaging industry, catapulting it into a new era of efficiency, reliability, and sustainability. By combining cutting-edge technology, user-friendly features, and a commitment to excellence, this revolutionary device ensures enhanced productivity, minimized wastage, and improved seal integrity. As the company continues to innovate and collaborate with industry partners, one can only anticipate further advancements in this groundbreaking technology. It is clear that with the Edge Sealing Machine, the packaging industry is primed for accelerated growth, solidifying its position as one of the most dynamic sectors in the global market.
Company News & Blog
Plastic Plate Machine Manufacturer and Supplier - Factory Direct
China Manufacturer and Supplier of Plastic Plate Machine - Factory DirectLooking for a reliable plastic plate machine manufacturer, supplier, or factory in China? Champion Machinery is your one-stop solution for high-quality machines designed for wholesale and OEM export. With a strong focus on global strategy and international markets, Champion Machinery has established a global agent network and promoted the Champion brand to localize its presence worldwide.Champion Machinery's footprint spans across Asia, Europe, Oceania, North and South America, Africa and the Middle East, showcasing its commitment to meeting the needs of customers around the world. The company's dedication to face-to-face communication with customers overseas has led to improved mutual understanding and enhanced service delivery.One of Champion Machinery's main products is the plastic plate machine, designed with precision and durability in mind. These advanced machines are ideal for producing high-quality plastic plates in a range of sizes and shapes, making them suitable for a variety of applications. The machines are designed to meet the needs of businesses of all sizes, from small-scale startups to large-scale manufacturers.Champion Machinery's plastic plate machines are not only efficient but also cost-effective, providing businesses with a reliable solution to increase their production capabilities. With advanced technology and automation, the machines ensure precision and efficiency in production. They are easy to operate, require minimal maintenance, and have a low failure rate, making them a reliable choice for businesses looking to streamline their manufacturing processes.In addition, Champion Machinery's plastic plate machines come with a guarantee of quality and after-sales service to ensure customer satisfaction. The machines are equipped with user-friendly features that make production a breeze, from loading raw materials to finished products. With advanced sensors and automated systems, the machines are also extremely safe, reducing the risk of accidents and injuries for staff while improving overall productivity.The company's commitment to providing innovative and high-quality machinery extends beyond the plastic plate machine. Champion Machinery offers an intelligent integrated system solution for material feeding, air supply, water supply, and power supply, as well as customized demand based on its technical strength and supply chain advantages.Customers who have invested in Champion Machinery's plastic plate machine have been highly satisfied with the product. Ms. Carlen Shu, a satisfied customer, commends the machine for its innovative design and efficiency in producing high-quality plastic plates. She highlights the machine's powerful motor and advanced technology, which allows for quick and efficient production, resulting in durable and long-lasting finished products.Another customer, Ms. Angela Her, praises the user-friendly interface of Champion Machinery's plastic plate machine, making it easy to operate for both personal and commercial use. The machine is constructed with high-quality materials, ensuring durability and long-term performance while producing plates with a smooth finish that is pleasing to the eyes.Champion Machinery's plastic plate machine is a must-have for anyone involved in the production of plastic plates and seeking highly efficient production processes.In conclusion, Champion Machinery's dedication to providing high-quality plastic plate machines and other advanced machinery is evident in its global presence and commitment to customer satisfaction. With a focus on innovation, precision, and durability, the company offers reliable and cost-effective solutions to meet the diverse needs of businesses worldwide. Contact Champion Machinery today to learn more about its plastic plate machines and take manufacturing capabilities to the next level!
Cutting-Edge Laminating Machine for Epe Foam Sheet Film: A Breakthrough in Manufacturing
Title: Cutting-Edge Laminating Machine Boosts Efficiency in EPE Foam Sheet Film ManufacturingIntroduction:In the fast-paced world of industrial manufacturing, companies are constantly seeking innovative solutions to enhance productivity and streamline operations. A noteworthy advancement in this regard comes in the form of the state-of-the-art EPE Foam Sheet Film Laminating Machine. Developed by a renowned industry leader, this cutting-edge machine introduces unprecedented efficiency and precision to the production of EPE foam sheet films.The EPE Foam Sheet Film Laminating Machine is poised to revolutionize the way manufacturers produce these versatile foam sheets, finding applications in numerous industries such as packaging, automobile, construction, and more. The elimination of manual processes and the seamless integration of technology make this machine an unrivaled asset for companies aiming to stay ahead of the competition.Unleashing Unmatched Efficiency:Driven by automation, the EPE Foam Sheet Film Laminating Machine significantly accelerates the production process, creating a ripple effect of increased efficiency throughout the manufacturing line. By eliminating manual labor, companies can now achieve higher output levels, faster turnaround times, and reduce overall production costs—a crucial factor in remaining competitive in today's market.The machine seamlessly integrates with existing production lines, allowing manufacturers to laminate EPE foam sheet films with a variety of materials, further expanding the applications of this versatile product. Its versatility enables it to handle various types of films, such as aluminum foil, kraft paper, and more, allowing manufacturers to cater to the diverse needs of their clientele.Uncompromising Precision and Quality:The EPE Foam Sheet Film Laminating Machine exhibits unparalleled precision in its lamination process, ensuring consistent and impeccable quality in the finished product. The advanced technology employed by the machine guarantees uniform distribution of adhesive, resulting in an ideal bond between the EPE foam and the films. This guarantees that the final product meets the highest standards of durability, protection, and aesthetics.With customizable settings and comprehensive control features, manufacturers can precisely adjust the machine to meet the specific requirements of different products. This adaptability enables businesses to explore various thicknesses, sizes, and combinations of materials, empowering them to cater to the unique needs of their customers. The incorporation of in-line inspection systems ensures quality control at every step, minimizing defective products and reducing wastage. By upholding the highest quality standards consistently, manufacturers can build a reputation for reliability and gain a competitive edge in the market.Investing in Sustainability:The EPE Foam Sheet Film Laminating Machine also exemplifies the growing significance of sustainability in manufacturing practices. By minimizing manual labor and reducing material wastage, the machine significantly contributes to ecological preservation. Moreover, its efficient energy consumption further amplifies its eco-friendly characteristics, enabling manufacturers to reduce their carbon footprint and contribute to a greener planet.Conclusion:The advent of the EPE Foam Sheet Film Laminating Machine marks a critical milestone in the evolution of foam sheet film manufacturing. With its unparalleled efficiency, precision, and adaptability, this cutting-edge technology propels businesses towards enhanced productivity, reduced costs, and increased customer satisfaction.By investing in this state-of-the-art machine, manufacturers can establish themselves as leaders in the industry, offering a comprehensive range of high-quality, durable, and customizable EPE foam sheet films. Furthermore, with its sustainable features, the machine not only boosts the company's bottom line but also contributes to the global commitment towards environmental conservation.As companies embrace the limitless possibilities presented by the EPE Foam Sheet Film Laminating Machine, they can look forward to a transformative future that encompasses optimized production processes, improved product quality, and lasting business success.
High-Quality Screws for Plastic Machinery and Equipment Manufacturing
: The Ultimate Guide to Plastic Screw ExtrudersAs plastic processing technology continues to advance, one of the most important components in plastic machinery is the screw. Screw technology has a huge impact on the efficiency and quality of plastic processing, which is why it’s important to choose a top-quality plastic screw extruder.In this blog, we’ll discuss everything you need to know about plastic screw extruders, from their components and types to the benefits they offer and how to choose the right one for your plastic processing equipment. So, let’s get started!What is a Plastic Screw Extruder?A plastic screw extruder is a type of plastic machinery that uses a screw to melt, mix, and move plastic materials through a heated barrel. The screw components typically include a feed section, a transition section, and a metering section. The feed section is responsible for feeding the plastic materials into the barrel, while the transition and metering sections control the melting and mixing of the plastic.There are two primary types of extruder screws: single-screw and twin-screw. Single-screw extruder screws are commonly used in applications where low to moderate plastic output rates are required. Twin-screw extruder screws, on the other hand, are ideal for high output rates and complex plastic processing applications.Components of a Plastic Screw ExtruderA plastic screw extruder is comprised of several key components, including:1. Barrel: The barrel is the primary component of the extruder that houses the plastic materials and screw. The barrel is heated to melt and mix the plastic materials, and it can be made from various materials such as steel, aluminum, or bronze.2. Screw: The screw is the component responsible for moving plastic materials through the extruder barrel. It’s composed of several sections, including the feed section, transition section, and metering section.3. Motor and Gearbox: The motor and gearbox work together to provide the power needed to drive the extruder screw. The gearbox provides the necessary torque to turn the screw, while the motor provides the power to the gearbox.4. Hopper: The hopper is the component responsible for storing and feeding plastic materials into the extruder barrel. The hopper has a capacity that can range from several pounds to several tons.5. Control System: The control system includes various components that regulate the extruder’s operation, such as temperature, speed, and pressure. It may include a touch screen interface that allows operators to adjust settings and monitor various parameters.Types of Plastic Screw ExtrudersThere are several types of plastic screw extruders, each designed for specific applications and plastic materials. Some of the most common types include:1. Single-screw extruders: As mentioned above, single-screw extruders are ideal for applications with low to moderate output rates. They’re commonly used for producing pipes, films, hoses, and profiles.2. Twin-screw extruders: Twin-screw extruders are the preferred choice for high-output, complex plastic processing applications. They can handle a wide range of materials and produce high-quality products, making them ideal for producing compounds, coatings, and high-performance polymers.3. Co-rotating and Counter-rotating Extruders: These extruders differ in the direction of the screws. Co-rotating extruders have screws that rotate in the same direction, while counter-rotating extruders have screws that rotate in opposite directions. Both types have their advantages and disadvantages, depending on the specific application requirements.Benefits of Plastic Screw ExtrudersThere are several benefits to using plastic screw extruders for plastic processing, including:1. Increased efficiency: Plastic screw extruders ensure that plastic materials are properly melted and mixed, resulting in higher efficiency and productivity of plastic processing.2. Consistent output quality: Plastic screw extruders provide consistent output quality that meets exact specifications.3. Better material control: Plastic screw extruders enable better control of plastic materials, resulting in better performance and longer product lifespan.4. Reduced costs: Plastic screw extruders are less expensive to operate than alternative plastic processing methods, making them a cost-effective choice for businesses.Choosing the Right Plastic Screw ExtruderTo choose the right plastic screw extruder for your plastic processing equipment, there are several factors to consider:1. Material type: Different materials require different extruder screw designs. Determine the exact materials you’ll be working with and choose an extruder that’s designed to handle those materials.2. Output requirements: Determine the required output rate and the level of melting and mixing required for the plastic materials.3. Extruder screw type: Choose between single-screw and twin-screw extruder screws based on your output rate and plastic processing requirements.4. Budget: Consider your budget and choose an extruder that meets your performance and operational requirements while remaining within your budget.ConclusionPlastic screw extruders are an essential component in plastic processing equipment, offering many benefits that result in increased efficiency, consistent output quality, better material control, and reduced costs. By choosing the right extruder screw for your plastic processing requirements, you can ensure high-quality output and improved long-term performance of your plastic processing equipment.
PVC Manufacturing Machine - Wholesale Supplier, and Factory in China
Champion Machinery, a leading manufacturer in China, is making waves in the global market with its top-notch PVC manufacturing machine. With a firm commitment to quality, durability, and performance, Champion Machinery is poised to revolutionize the PVC manufacturing industry worldwide.The PVC manufacturing machine offered by Champion Machinery is designed with cutting-edge technology and premium-quality materials, ensuring top-notch performance and reliability. This state-of-the-art machine is capable of producing high-quality PVC products of any shape and size with ease and efficiency.One of the key features of the PVC manufacturing machine is its fast production rate, allowing manufacturers to significantly increase their overall production capacity. Whether it's pipes, tubing, or other PVC products, the PVC manufacturing machine from Champion Machinery is the perfect solution for all PVC manufacturing needs.The team at Champion Machinery is dedicated to exceeding customer expectations, prioritizing customer satisfaction above all else. With a focus on providing high-quality equipment at an affordable price, Champion Machinery is a trusted supplier for those looking to elevate their PVC manufacturing operations.Additionally, Champion Machinery offers an array of other products including Vacuum forming, Recycling plastic, Sheet film Line, Blow/injection molding machine, EPE foam machine, Hydraulic cutting machine, Air compressor, Screw compressor, Chiller, Hopper dryer, Crusher, Mixer, and Auto loader. These products are integrated into an intelligent system that provides solutions for Material Feeding, Air Supply, Water Supply, and Power Supply, meeting customized demands based on technical strength and supply chain advantages.To support their international presence, Champion Machinery has established a global agent network and actively promotes and localizes the Champion brand in various markets. They have a well-established presence in numerous regions worldwide, including Asia, Europe, Oceania, North and South America, Africa, and the Middle East.The success of the PVC manufacturing machine from Champion Machinery is reflected in the positive feedback from satisfied customers. Ms. Carlen Shu, a user of the PVC manufacturing machine, highlighted its high efficiency, precision manufacturing capabilities, and consistent quality across all products. She also praised its durable construction and user-friendly interface, making it a wise investment for any PVC manufacturer.Another user, Ms. Angela Her, shared that the PVC manufacturing machine exceeded her expectations, with top-notch quality and efficiency. She emphasized its ease of use, durability, and efficiency, making it a worthwhile investment for anyone in the industry.Looking ahead, Champion Machinery is set to continue its global expansion and continue to provide innovative solutions for PVC and other manufacturing needs. With a strong focus on quality, customer satisfaction, and technological advancement, Champion Machinery is well-positioned to become a leader in the global manufacturing industry.For those looking to take their PVC manufacturing to the next level, Champion Machinery is the supplier to trust. Contact them today to learn more about the PVC manufacturing machine and how it can benefit your business. With a track record of excellence and a dedication to customer satisfaction, Champion Machinery is a name to remember in the world of manufacturing.
Top Injection Molding Press Manufacturer & Supplier in China | Wholesale Solutions at Factory Price
Champion Machinery Expands Global Reach with High-Quality Injection Molding PressChampion Machinery has been making waves in the international market with its top-quality Injection Molding Press. As the leading manufacturer, supplier, and factory of high-performance injection molding presses in China, Champion Machinery is committed to delivering outstanding precision, reliability, and efficiency in various industrial applications.The injection molding presses offered by Champion Machinery are crafted from the finest materials and components, ensuring optimal durability and competitiveness. With a wide range of sizes available, from small to large, Champion Machinery provides solutions for molding different types of products and materials to meet the diverse needs of businesses worldwide.Equipped with advanced control systems, Champion Machinery's injection molding presses allow operators to easily adjust the parameters of the molding process for optimal results. Not only are these presses high-performing, but they are also energy-efficient, reducing electricity consumption and lowering operation costs and carbon footprint.Champion Machinery takes pride in its commitment to high-quality products and customer satisfaction, offering comprehensive after-sales services that include technical support, maintenance, and repair. This ensures seamless and uninterrupted operation of the injection molding presses for businesses around the globe.One of the outstanding features of Champion Machinery's Injection Molding Press is its ability to produce a wide range of high-quality plastic products with precision and accuracy. Its state-of-the-art technology ensures uniformity and consistency in every product, providing exceptional results. The press's robust construction and efficient operation guarantee long-lasting performance for years, making it the ideal solution for producing various plastic components such as automotive parts, electronic appliances, and medical equipment.To further solidify its dedication to customer satisfaction, Champion Machinery emphasizes excellent customer service, guiding clients through every step of the manufacturing process. This commitment to quality and efficiency has earned Champion Machinery a reputation as a reliable and efficient manufacturer of top-quality plastic products.The global success of Champion Machinery's Injection Molding Press is further evidenced by the glowing reviews from customers like Ms. Carlen Shu and Ms. Angela Her. They both attest to the press's reliability, efficiency, and cost-effectiveness, making it a valuable investment that delivers exceptional value and performance. Their praise for the press's precise molding capabilities and consistency in delivering uniform parts further solidifies its reputation as an outstanding product revolutionizing the manufacturing industry.Champion Machinery's global strategy has led to the establishment of a robust agent network, promoting and localizing the Champion brand. With a presence in Asia, Europe, Oceania, North and South America, Africa, and the Middle East, Champion Machinery is making its mark in the global market.In addition to the Injection Molding Press, Champion Machinery offers a comprehensive product system, including Vacuum Forming, Recycling Plastic, Sheet Film Line, Blow/Injection Molding Machine, EPE Foam Machine, Hydraulic Cutting Machine, Air Compressor/Screw Compressor, Chiller, Hopper Dryer, Crusher, Mixer, Auto Loader - all in one intelligent integrated system solution for material feeding, air supply, water supply, and power supply, meeting the customized demands of businesses worldwide.In conclusion, Champion Machinery's Injection Molding Press is a must-have for any manufacturing business, offering exceptional value, reliability, cost-effectiveness, and high-quality production. With its global reach and commitment to customer satisfaction, Champion Machinery is a driving force in the international market, delivering cutting-edge solutions for businesses worldwide. Contact Champion Machinery today to experience the excellence of their injection molding press and integrated system solutions.
Vertical Cutting Machine for Efficient and Precise Cutting
EPE Vertical Cutting Machine Revolutionizes Foam Cutting ProcessFoam materials have become an integral part of various industries, including packaging, automotive, construction, and more. With the increasing demand for precision-cut foam products, the need for efficient cutting machines has also risen. In response to this demand, [Company Name] has introduced a groundbreaking solution – the EPE Vertical Cutting Machine.[Company Name] is a leading provider of cutting-edge machinery and equipment for the foam industry. With years of experience and expertise in foam processing technology, the company has established a strong reputation for delivering innovative solutions that meet the evolving needs of its customers. The latest addition to their product lineup, the EPE Vertical Cutting Machine, is set to revolutionize the foam cutting process with its advanced features and superior performance.The EPE Vertical Cutting Machine is designed to streamline the cutting process for foam materials, offering unmatched precision and efficiency. With its state-of-the-art vertical cutting technology, the machine can handle a wide range of foam products with varying thickness and density, delivering clean and accurate cuts every time. This makes it an ideal solution for manufacturers and businesses looking to enhance their foam cutting operations and improve the quality of their products.One of the key highlights of the EPE Vertical Cutting Machine is its user-friendly design, which makes it easy to operate and maintain. Equipped with intuitive controls and a robust cutting mechanism, the machine is capable of delivering consistent results while minimizing downtime and operational complexities. This not only improves productivity but also reduces the overall cost of production, making it a cost-effective investment for businesses of all sizes.Moreover, the EPE Vertical Cutting Machine is built to meet the highest standards of quality and reliability. Constructed with durable materials and precision-engineered components, the machine is built to withstand the rigors of continuous use in industrial settings. This ensures long-term performance and minimal maintenance requirements, providing a reliable cutting solution that businesses can depend on for years to come.In addition to its cutting-edge features, the EPE Vertical Cutting Machine also offers a range of customization options to suit specific cutting requirements. Whether it's a custom foam shape, size, or thickness, the machine can be tailored to meet the unique needs of different applications. This flexibility allows businesses to expand their product offerings and cater to a wider range of customer demands, ultimately driving growth and profitability.As a trusted provider of foam cutting solutions, [Company Name] also offers comprehensive support services for the EPE Vertical Cutting Machine. From installation and training to ongoing technical assistance, the company is committed to ensuring that its customers maximize the potential of their investment and achieve optimal results. This customer-centric approach has earned [Company Name] a loyal and satisfied customer base, positioning them as a preferred partner for businesses in the foam industry.With its innovative design, advanced capabilities, and unwavering commitment to customer satisfaction, the EPE Vertical Cutting Machine is poised to set new benchmarks in foam cutting technology. As industries continue to evolve and demand higher standards of quality and efficiency, this cutting-edge solution from [Company Name] is well-positioned to meet the evolving needs of the market and empower businesses to stay ahead of the competition.In conclusion, the launch of the EPE Vertical Cutting Machine represents a significant milestone for [Company Name] and the foam industry as a whole. With its game-changing features and unparalleled performance, the machine is set to elevate the standards of foam cutting, setting new benchmarks for precision, efficiency, and reliability. As businesses strive to deliver superior foam products and enhance their competitiveness, the EPE Vertical Cutting Machine stands out as a transformative solution that promises to shape the future of foam processing.
Understanding the Importance of Injection Speed in Injection Molding
Injection Speed In Injection MoldingInjection molding is a widely used manufacturing process for producing parts by injecting material into a mold. One of the crucial factors that determine the quality and efficiency of the process is the injection speed. Injection speed refers to the speed at which the material is injected into the mold. It plays a vital role in the overall production process, affecting the final product's quality, surface finish, and overall cycle time.Leading in the industry is {} (Company), a global leader in industrial manufacturing solutions. The company has a proven track record of providing high-quality injection molding machines and solutions to various industries worldwide.One of the key features of {}'s injection molding machines is their ability to control and adjust injection speed. This allows for a precise and efficient molding process, resulting in high-quality and consistent parts production.With the injection speed being a critical factor in the injection molding process, {} has developed state-of-the-art technology to ensure optimal performance. The company's injection molding machines are equipped with advanced control systems that allow operators to precisely adjust and monitor the injection speed, providing flexibility and control over the production process.Furthermore, {}'s injection molding machines are designed to achieve high injection speeds without compromising on the quality of the final product. This is achieved through innovative design and engineering, as well as the use of high-quality materials and components.The ability to adjust injection speed according to the specific requirements of each part and material is crucial in achieving the desired results. {}'s injection molding machines offer a wide range of injection speed options, allowing for versatility in production and ensuring that each part is manufactured with precision and accuracy.In addition to providing high-quality injection molding machines, {} also offers comprehensive support and solutions to its customers. The company's team of experts is dedicated to helping businesses optimize their production processes, providing guidance on injection speed optimization and other factors that can impact the overall efficiency and quality of production.{}'s commitment to innovation and excellence has made it a trusted partner for businesses looking to enhance their injection molding capabilities. With its advanced injection molding machines and expertise in injection speed control, {} continues to set the standard for quality and performance in the industry.In conclusion, injection speed is a critical factor in the injection molding process, and {} has proven itself as a leader in providing high-quality injection molding machines with advanced injection speed control capabilities. With its commitment to innovation and excellence, {} is a valuable partner for businesses looking to achieve optimal results in their injection molding operations.
Quality Second Hand Blow Moulding Machines Offered at Competitive Prices
Title: Second Hand Blow Moulding Machine: Cost-Effective Solution for Efficient Plastic ProductionIntroduction:In the ever-evolving world of manufacturing, the demand for plastic products continues to soar. To meet this growing need, the availability of cost-effective solutions has become crucial for businesses. Acknowledging this, Company XYZ, a reputable name in the manufacturing industry, has introduced second-hand blow moulding machines. These machines not only offer an economic alternative but also ensure enhanced productivity without compromising on quality. By launching this new venture, Company XYZ aims to revolutionize the production process while minimizing environmental impact.Paragraph 1: Understanding the significance of effective plastic production in various sectors, Company XYZ has partnered with leading industrial manufacturers to refurbish used blow moulding machines. By removing proprietary branding, they offer a range of reliable, high-performance equipment at a fraction of the price of new machines. This strategic move aims to cater to small and medium-sized enterprises, providing them with access to advanced technology without straining their budgets.Paragraph 2:Company XYZ's second-hand blow moulding machines undergo a rigorous refurbishing process before being made available for sale. Combining their expertise with the expertise of their partner manufacturers, Company XYZ ensures that the machines undergo meticulous inspection, repair, and replacement of any faulty components. The machines are then calibrated to ensure optimum performance, meeting industry standards. This stringent refurbishment process guarantees that the equipment functions as good as new, offering businesses a reliable and cost-effective plastic production solution.Paragraph 3: One of the key advantages of purchasing a second-hand blow moulding machine from Company XYZ lies in the company's commitment to exceptional customer service. Alongside the sale, Company XYZ provides comprehensive support and training to assist businesses in integrating the new equipment into their manufacturing processes smoothly. By offering technical guidance and troubleshooting assistance, they ensure that customers derive maximum value from their investment.Paragraph 4:In addition to the economic benefits, Company XYZ's second-hand blow moulding machines also contribute to reducing environmental impact. By extending the lifecycle of these machines, Company XYZ actively promotes sustainable manufacturing practices. This approach aligns with the increasing demand from consumers and regulatory bodies for companies to adopt eco-friendly solutions. Companies opting for second-hand machinery not only save on costs but also make a positive environmental contribution by reducing overall waste and resource consumption.Paragraph 5:The launch of the second-hand blow moulding machines aligns with Company XYZ's vision to reshape the plastic production landscape. By offering a cost-effective solution, they aim to foster innovation and competitiveness among smaller players in the market. Moreover, the availability of reliable refurbished equipment enables companies to stay ahead of the curve in meeting the ever-changing consumer demands efficiently and sustainably.Conclusion:Company XYZ's introduction of second-hand blow moulding machines revolutionizes the plastic production industry by offering businesses an economic and reliable alternative. By refurbishing and rejuvenating used equipment, combined with their commitment to exceptional customer service and sustainability, Company XYZ positions itself as a game-changer for small and medium-sized manufacturing enterprises. As the demand for plastic products continues to surge, these cost-effective solutions pave the way for a more sustainable and efficient future.
Fully Automatic Production Circular Saw for High Precision Cutting
story:A Fully Automatic Production Circular Saw is now available from one of the top providers in the industry, Kasto. This new circular saw promises high cutting performance and exceptionally long blade life. The Heavy machine base and high-quality components are the foundation for these superior cutting capabilities. The saw is equipped with a frequency-controlled 18 kW three phase motor that has a reliable high-performance spur gear system. In addition, its pre-tensioned ball screw spindle ensures minimal ancillary time and automatic adaptation of feed.Carbide sawing has been around since the 1930s when sawing non-ferrous materials, such as aluminum, brass, plastic, and wood, became a necessity. The carbide-tipped circular saw blades revolutionized the way these materials were cut, making it possible to achieve faster cutting speeds and produce cleaner, more accurate cuts. However, cutting ferrous material continued to present a challenge. It was not until the development of the feed system that cutting ferrous material became easier. The feed system, which consists of either a hydraulic cylinder or a ball screw with a gear reducer, powered by a servo motor, enabled the carbide saw blades to cut through ferrous material with ease. The Tsune Circular Saw, available from Clinton Aluminum, is one example of a specialized saw designed specifically for cutting aluminum. The saw is equipped with a six-inch diameter blade, brass blade guides, and a ball screw gripper feed, making it precise and accurate in its cutting capabilities. The saw can cut a section of aluminum that is 150 millimeters in length with a tolerance of one-tenth of a millimeter.Clinton Aluminum is one of the leading suppliers of aluminum products in the industry, providing a wide range of aluminum products to businesses and manufacturers across the country. Their commitment to quality and excellence is evident in the products they carry and the equipment they use. Whether you are looking for a fully automatic production circular saw, or a specialized saw designed for cutting aluminum or other materials, Clinton Aluminum has the products and services to meet your needs. With their knowledgeable staff, commitment to customer service and quality products, they stand out as a reliable and trusted name in the industry. If you are looking to boost efficiency and productivity in your manufacturing process, the fully automatic production circular saw from Kasto or the specialized Tsune Circular Saw from Clinton Aluminum are excellent options to consider. With their advanced technology and precision cutting capabilities, these saws are sure to provide the performance and quality you need to meet the demands of your business.
Manufacturer & Supplier of Injection Molding Machine - Factory Direct Sales
Champion Machinery Expands Global Reach with Top-Quality Injection Molding MachinesChampion Machinery has been making waves in the international market with its commitment to providing top-quality injection molding machines. With a focus on expanding its global presence, the company has established a strong agent network and has been actively promoting the Champion brand on a worldwide scale.The company's dedication to engaging with customers on a personal level has been a driving force behind its success in the global market. By making regular visits to customers overseas, Champion Machinery has been able to foster strong relationships and improve mutual understanding, leading to enhanced customer service and satisfaction.As part of its product offerings, Champion Machinery boasts a wide range of high-quality machines, including vacuum forming, recycling plastic, sheet film lines, blow/injection molding machines, EPE foam machines, hydraulic cutting machines, air compressors, screw compressors, chillers, hopper dryers, crushers, mixers, and auto loaders. With a focus on providing intelligent integrated system solutions for material feeding, air supply, water supply, and power supply, the company's technical expertise and supply chain advantages allow it to efficiently meet customized demands from its customers.One of the company's standout products, the Injection Molding Machine, has been garnering attention for its exceptional performance and versatility. Designed to produce high-quality products with precision, the Injection Molding Machine utilizes the latest technology in the injection molding process to create complex geometries with outstanding quality and consistency. Its compact and innovative design allows for space-saving and easy mobility, making it a practical choice for manufacturing facilities of all sizes.The Injection Molding Machine features a variety of hydraulic controls, including five pressure and three position control channels, allowing for effortless customization to meet specific molding requirements. With a wide range of injection capacity, ranging from 1 to 100 grams, the machine can easily produce both small and large components with ease. Engineered with top-quality materials, the machine offers impressive durability, stability, and longevity, backed by a team of knowledgeable experts who provide excellent technical support and customer service.Customer reviews of the Injection Molding Machine speak to its high performance and reliability. Ms. Carlen Shu, a satisfied customer, praised the machine for its versatile applications and high-performance hydraulic system, making it an excellent choice for businesses seeking a reliable and efficient injection molding machine. Ms. Angela Her commended the machine for its compact design, ease of use, precision in producing high-quality parts, and seamless hydraulic pressure system, making it a top contender in the market.Looking to the future, Champion Machinery remains committed to its global strategy and endeavors to continue exploring international markets. With a strong foundation in place, the company's footprint covers regions across Asia, Europe, Oceania, North and South America, Africa, and the Middle East, solidifying its position as a leading provider of top-quality injection molding machines on a global scale.For businesses seeking a dependable injection molding machine, Champion Machinery's Injection Molding Machine stands out as a reliable and high-quality choice. With its commitment to excellence and customer satisfaction, the company is poised to continue making significant strides in the global market.