Efficient Plastic Egg Tray Making Machine in News: Key Features and Benefits
By:admin
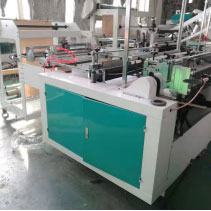
Introduction:
In response to the growing demand for sustainable and eco-friendly packaging solutions, an innovative plastic egg tray making machine has been introduced by a prominent industry player. This advanced technology is poised to revolutionize the poultry industry by successfully addressing the concerns of environmental degradation caused by traditional packaging methods. With its ability to produce high-quality, durable, and recyclable egg trays on a large scale, this machine aims to create a positive impact on both the poultry industry and the environment as a whole.
Body:
1. Background on the Plastic Egg Tray Making Machine:
The plastic egg tray making machine is a cutting-edge technology developed by [Company Name], a pioneer in the field of eco-friendly packaging solutions. This state-of-the-art machinery is designed to convert waste plastic materials into robust, lightweight, and biodegradable egg trays.
2. Key Features and Benefits:
The machine boasts several key features that set it apart from traditional egg tray manufacturing methods. Firstly, it operates using recyclable plastics, reducing environmental pollution caused by non-biodegradable materials. Secondly, it adopts an efficient manufacturing process that guarantees the production of high-quality egg trays at a fast pace, ensuring a steady supply of packaging for the poultry industry. Finally, the trays produced by this machine are biodegradable, recyclable, and can be repurposed for various other purposes, thus promoting a circular economy.
3. Positive Impact on the Poultry Industry:
The introduction of the plastic egg tray making machine is set to revolutionize the poultry industry in multiple ways. Firstly, it addresses the issue of limited supply of high-quality packaging materials by providing a consistent and readily available source of egg trays. This ensures that egg producers can deliver their products safely to market, preventing potential damage or loss during transportation.
Additionally, the recyclability and durability of the trays produced by this machine significantly reduce packaging costs for the farmers. Its high production capacity also ensures economies of scale, leading to cost reduction in the long run.
4. Environmental Implications:
One of the most notable benefits of the plastic egg tray making machine is its ecological impact. By utilizing recyclable plastics in producing egg trays, it mitigates the environmental risks posed by conventional materials such as Styrofoam or cardboard. Moreover, the trays are biodegradable, ensuring that they decompose naturally without contributing to pollution or waste accumulation. This sustainable approach not only reduces the carbon footprint associated with traditional packaging but also aligns with global initiatives to combat climate change and reduce plastic waste.
5. Future Prospects and Expansion:
With extensive market research and testing, it is expected that the plastic egg tray making machine will witness a significant demand worldwide. Its high production capacity will cater to the needs of large-scale poultry operations, ensuring a streamlined and efficient packaging process.
Moreover, with the machine's versatility and adaptability, there is potential for its application beyond the poultry industry. For instance, it can be used to manufacture trays for other agricultural products or explore possibilities in the food service and retail sectors. This diversification opens up new revenue streams for both the company and its customers.
Conclusion:
The advent of the plastic egg tray making machine represents a significant breakthrough in the field of sustainable packaging solutions for the poultry industry. With its ability to efficiently convert recyclable plastics into high-quality egg trays, it not only meets the packaging demands of egg producers but also significantly reduces the industry's carbon footprint. This innovative machinery has the potential to transform the poultry industry while offering an eco-friendly alternative to traditional packaging methods. As we move towards a more sustainable future, the plastic egg tray making machine proves to be a game-changer that paves the way for other industries to follow suit in adopting eco-conscious practices.
Company News & Blog
New Development in Injection Molding Technology for Resin 3D Printed Molds
- Baschz - Lamball Bakra - open source - injection molder - resin - 3D printed molds - brand name removedDesktop Injection Molding: Innovation at Your FingertipsIn today's fast-evolving world, businesses are constantly on the lookout for ways to streamline their production processes and enhance their competitiveness. Desktop injection molding has emerged as a game-changing technology that allows small businesses and individuals to cost-effectively produce high-quality plastic parts in-house. In this blog, we'll explore the basics of desktop injection molding technology and showcase the innovative work of Baschz, a Lamball Bakra testing the boundaries of what's possible.What Is Desktop Injection Molding?At its core, injection molding is a manufacturing process in which molten plastic is injected into a mold cavity, cooled and solidified, and then ejected as a finished part. This technique is widely used in manufacturing for producing plastic components in large volume. However, traditional injection molding machines are expensive, bulky, and require significant setup time.Desktop injection molding, also known as micro injection molding, is a scaled-down version of traditional injection molding, designed for low-volume production and prototyping. It involves using a smaller, benchtop machine that can fit on a desk or table, and running it with smaller quantities of thermoplastic resins. Desktop injection molding enables faster turnaround times, greater design flexibility, and significantly lower startup costs.Meet Baschz: Pushing the Boundaries of Desktop Injection MoldingBaschz is a Lamball Bakra who has been exploring the world of desktop injection molding as a creative outlet. Over the past few months, he has built and tested two different open-source injection molding machines, using molds he has 3D printed in resin.Baschz's first machine was built from an open-source design and cost around $600 to assemble. His second machine is an improved version, which he built using a combination of off-the-shelf components and custom parts. He has been experimenting with a variety of thermoplastic resins and is currently using a recycled plastic blend.Through his testing, Baschz has learned that while desktop injection molding is not perfect, it does offer significant advantages over traditional injection molding. He notes that it's easy to make minor changes to molds on the fly, and the initial setup is relatively simple. Baschz also highlights the ability to use recycled plastics, which reduces the environmental impact of his creations.Looking Ahead: The Future of Desktop Injection MoldingAs the technology behind desktop injection molding continues to evolve, we can expect to see more entrepreneurs and small businesses leveraging this game-changing technology to enhance their operations. From fast turnaround times to the ability to make small batches of custom parts, desktop injection molding is opening up new possibilities for innovation.Whether you're a Baschz looking to push the boundaries of what's possible or a small business looking for ways to streamline your operations, desktop injection molding is a powerful tool that can help you achieve your goals. With its scalability and flexibility, this technology stands to revolutionize the manufacturing industry and make it more accessible to a broader range of creators.
High-Quality Plastic Extruder Screw Manufacturer in China - Supplier & Factory
Champion Machinery is Making Waves in the Plastics IndustryChampion Machinery, a leading company in China, is making significant strides in the plastics industry with their top-quality products and innovative designs. With a strong focus on global expansion and customer satisfaction, the company has positioned itself as a trusted partner for businesses worldwide.Establishing Global ReachChampion Machinery has set its sights on becoming a global player in the plastics manufacturing industry. Through a well-established agent network and localized marketing efforts, the company has successfully promoted its brand and built strong relationships with customers across the globe. With a presence in Asia, Europe, Oceania, North and South America, Africa, and the Middle East, Champion Machinery has truly made its mark on the international stage.Product OfferingsChampion Machinery offers a diverse range of products designed to cater to the various needs of the plastics manufacturing industry. Their product system includes the Vacuum Forming, Recycling Plastic, Sheet Film Line, Blow/Injection Molding Machine, EPE Foam Machine, Hydraulic Cutting Machine, and an array of auxiliary equipment such as Air Compressors, Screw Compressors, Chillers, Hopper Dryers, Crushers, Mixers, and Auto Loaders. This comprehensive range of products provides customers with intelligent integrated solutions for material feeding, air supply, water supply, and power supply, allowing for maximum efficiency and customization based on specific technical requirements.Focus on Quality and InnovationWithin the product range, one standout product is the Plastic Extruder Screw. This cutting-edge product is revolutionizing the plastics industry with its exceptional quality and innovative design. Champion Machinery's commitment to superior strength, longevity, and efficiency is reflected in the meticulous crafting of the plastic extruder screw using premium materials. This ensures that the screws can handle various plastic materials, providing excellent precision and uniformity during the extrusion process. The company has implemented strict quality control measures at every stage of the manufacturing process to guarantee that each plastic extruder screw leaving the factory meets the highest standards and surpasses customer expectations.Customer Satisfaction and SupportAt Champion Machinery, customer satisfaction is the top priority. The company places great emphasis on providing comprehensive support services, including technical assistance and personalized consultations, to ensure that customers achieve optimal results with their products. The goal is to help businesses upgrade their manufacturing processes and stay ahead of the competition, and Champion Machinery is dedicated to making this vision a reality for all of their customers.TestimonialsCustomers who have experienced Champion Machinery's products have shared positive feedback, commending the exceptional performance and reliability of the plastic extruder screw. Users have highlighted the screw's durability, efficiency, and ease of use, as well as its ability to handle various types of plastic materials with precision and consistency.Looking AheadChampion Machinery continues to push the boundaries of what is possible in the plastics manufacturing industry. With a strong focus on quality, innovation, and customer satisfaction, the company is set to further solidify its position as a leader in the global market. By providing cutting-edge products and comprehensive support services, Champion Machinery is helping businesses around the world achieve new levels of success in plastic extrusion and manufacturing.In conclusion, Champion Machinery's dedication to quality, innovation, and customer satisfaction has set a new standard for the industry. With a global outlook and a comprehensive range of products, the company is well-positioned to lead the way in the ever-evolving plastics manufacturing landscape. Businesses seeking reliable, high-quality solutions for plastic extrusion and manufacturing need look no further than Champion Machinery.
High-Quality Strong Granulator Manufacturer & Supplier in China - Top Factory for Granulator Equipment
Champion Machinery Expands Global Presence with Strong Granulator IntroductionChampion Machinery, a leading manufacturer and supplier in the plastic processing industry, has announced the launch of its latest product - the Strong Granulator. This robust and powerful machine is designed to efficiently crush and recycle various plastic materials, offering unparalleled performance and durability.The Strong Granulator is the result of Champion Machinery's commitment to innovation and quality. With its powerful motor and precision cutting blades made of high-quality steel, this granulator can easily shred even thick and bulky items such as pipes, bottles, and containers into small and easily manageable pieces. The machine also comes equipped with safety features such as overload protection and a safety switch to ensure safe and reliable operation.The compact size and low noise level of the Strong Granulator make it ideal for use in small workshops or production lines, offering a comfortable working environment without compromising on performance. This versatile machine is suitable for a wide range of applications including recycling, waste management, and manufacturing.One of the key features of the Strong Granulator is its user-friendly design, making it easy to operate and maintain. The granulator is also designed with safety in mind, featuring several safety measures such as an emergency stop button and soundproof enclosure to reduce noise pollution.The introduction of the Strong Granulator underscores Champion Machinery's commitment to providing high-quality and cost-effective solutions for cutting and shredding requirements. The company has built a strong reputation for its technical expertise and reliable performance, making it a trusted partner for businesses looking to improve their operations and efficiently recycle waste materials.Customers have praised the Strong Granulator for its unparalleled crushing power and versatility. Ms. Carlen Shu, a user of the Strong Granulator, commented, "The Strong Granulator is hands down the best granulator I have ever used. It has unparalleled crushing power, making quick work of even the toughest materials. Whether you're in the plastics industry or the pharmaceutical industry, this granulator is a game-changer."In addition to the Strong Granulator, Champion Machinery offers a comprehensive product system including Vacuum forming, Recycling plastic, Sheet film Line, Blow/injection molding machine, EPE foam machine, Hydraulic cutting machine, and a range of auxiliary equipment such as air compressors, screw compressors, chillers, and crushers. The company also provides intelligent integrated system solutions for material feeding, air supply, water supply, and power supply, as well as customized solutions based on its technical strength and supply chain advantages.Champion Machinery has been actively expanding its presence in the global market, establishing a strong agent network and promoting its brand internationally. The company's global footprint covers regions including Asia, Europe, Oceania, North and South America, Africa, and the Middle East. Through face-to-face communication and visits to customers overseas, Champion Machinery has been able to improve mutual understanding and provide excellent service to its customers worldwide.With the introduction of the Strong Granulator and its comprehensive product system, Champion Machinery is well-positioned to meet the evolving needs of the plastic processing industry and offer leading-edge solutions to businesses around the world. Contact Champion Machinery today to learn more about the Strong Granulator and how it can benefit your business.
Nylon CNC Manufacturer: High-Quality Precision Machining Solutions for Nylon Components
Champion Machinery Expands Reach to International Markets with High-Quality Nylon CNC Machining ServicesWith a focus on expanding its global presence, Champion Machinery has increased its efforts to explore international markets and establish a strong network of agents around the world. As part of this strategy, the company has been promoting its brand and localizing its services to better serve customers in various regions. Through face-to-face communication and visits to customers overseas, Champion Machinery has been able to strengthen its relationships and improve service to customers worldwide. The company's reach now spans across Asia, Europe, Oceania, North and South America, Africa, and the Middle East, demonstrating its commitment to providing high-quality products and services on a global scale.One of Champion Machinery's main products is its "many" Product System, which includes a range of equipment and machinery to meet the diverse needs of its customers. This product system consists of six series of products, including Vacuum Forming, Recycling Plastic, Sheet Film Line, Blow/Injection Molding Machine, EPE Foam Machine, Hydraulic Cutting Machine, and a range of auxiliary equipment such as Air Compressors, Screw Compressors, Chillers, Hopper Dryers, Crushers, Mixers, and Auto Loaders. These solutions provide an all-in-one intelligent integrated system for material feeding, air supply, water supply, and power supply, allowing customers to efficiently meet their customized requirements based on Champion Machinery's technical strength and supply chain advantages.In line with its commitment to delivering high-quality products and services, Champion Machinery has introduced a range of precision Nylon CNC machining services at its factory in China. Leveraging state-of-the-art machinery and skilled technicians, the company specializes in the CNC machining of nylon, ensuring a high level of accuracy, consistency, and quality in every order. Whether customers require simple or complex shapes, Champion Machinery can deliver nylon parts and components in a wide range of sizes and quantities.The company's advanced technology and expertise in CNC machining have enabled it to produce complex shapes and designs for its Nylon products, which are ideal for a variety of applications in industries such as automotive, aerospace, and medical. Nylon is known for its unique properties, including high strength, lightweight nature, excellent resistance to wear, chemicals, and heat, as well as resistance to corrosion and low friction, making it suitable for applications that require high lubricity.Champion Machinery's dedication to providing exceptional service, competitive pricing, fast turnaround, and unparalleled expertise ensures that every part produced meets or exceeds customer expectations. The company's experienced engineers and technicians are highly skilled in CNC machining and quality control, guaranteeing that its Nylon products meet the strictest requirements and specifications.Customers who have utilized Champion Machinery's Nylon CNC machining services have praised the company for its innovative and high-quality products. Ms. Carlen Shu, a satisfied customer, highlighted the precision and accuracy of the CNC machining process, which allows for the production of high-quality nylon components with utmost precision and consistency. Another customer, Ms. Angela Her, commended the mechanical properties of nylon and its suitability for industrial and commercial applications, particularly in industries such as automotive, aerospace, and medical.As Champion Machinery continues to expand its global reach and offer high-quality products and services, customers can expect to benefit from the company's dedication to innovation, precision, and customer satisfaction. Contact Champion Machinery today to learn more about its Nylon CNC machining capabilities and how it can help your business succeed.
High-Quality Pet Bottle Recycling To Fiber Machine Manufacturer and Supplier in China - Factory Direct Prices Available
China-based Manufacturer Leads the Way in Sustainable Recycling SolutionsIn a world where environmental sustainability is a growing concern, Champion machinery is taking the lead in offering innovative and eco-friendly solutions for recycling plastic bottles. With a strong focus on international markets, the company has established a global agent network and promoted its brand on a localized level. Champion machinery has made its mark across the globe, with a presence in Asia, Europe, Oceania, North and South America, Africa, and the Middle East.One of Champion's main products, the Pet Bottle Recycling to Fiber Machine, has garnered attention for its ability to transform waste plastic bottles into high-quality fiber. This revolutionary machine offers a cost-effective solution for businesses and individuals looking to reduce their carbon footprint and contribute to a cleaner environment. By shredding and separating plastic bottles into small fiber particles, the machine provides a sustainable alternative for a wide range of industries, including textile manufacturing, construction, and insulation materials.With a strong emphasis on energy efficiency, the Pet Bottle Recycling to Fiber Machine ensures minimal energy consumption, further reducing its environmental impact. The entire process is designed to handle large volumes of plastic waste, effectively reducing the amount of plastic that ends up in landfills and oceans.Customer testimonials speak to the efficiency and effectiveness of the machine, with one satisfied customer, Ms. carlen shu, commending the product for its ease of use and its ability to turn waste into valuable fiber. She notes the machine's durability and cost-effectiveness as significant benefits, making it a worthwhile investment for businesses and individuals alike.Another customer, Ms. Angela Her, highlights the machine's contributions to reducing plastic waste and its output quality, making it a viable option for manufacturers looking to reduce their carbon footprint.Champion machinery's commitment to sustainability extends beyond the Pet Bottle Recycling to Fiber Machine, with a range of other innovative products designed to offer integrated system solutions for material feeding, air supply, water supply, and power supply. The company's technical strength and supply chain advantages enable Champion to efficiently meet the customized demands of its customers.As the company continues to expand its presence in the global market, it remains dedicated to face-to-face communication with customers overseas, further improving mutual understanding and service delivery. This approach has helped Champion machinery build strong relationships with its international clientele, paving the way for continued success in the sustainable recycling industry.With its innovative product offerings and commitment to global sustainability, Champion machinery is positioning itself as a leader in eco-friendly recycling solutions. The company's dedication to creating a cleaner environment and reducing the impact of plastic waste is evident in its continued efforts to provide top-quality, sustainable products for businesses and individuals worldwide.For those looking to make a positive impact on the environment while maximizing their profits, Champion machinery's Pet Bottle Recycling to Fiber Machine stands as a testament to the company's vision for a more sustainable future. With a focus on efficiency, cost-effectiveness, and environmental responsibility, Champion machinery is paving the way for a greener, more sustainable world.
PVC Sheet Cutting Machine Manufacturer, Supplier, and Factory in China | High-Quality Cutting Solutions
Champion Machinery Expands International Presence with Top-Quality PVC Sheet Cutting MachineChampion Machinery, a leading manufacturer and supplier of industrial machinery, has announced its commitment to expanding its global presence through the promotion and localization of its top-quality PVC Sheet Cutting Machine. With a strategic focus on exploring international markets and establishing a robust agent network, Champion Machinery is poised to deliver its cutting-edge solutions to customers around the world.The company's global strategy includes a dedicated effort to cultivate relationships with customers through face-to-face communication, demonstrating Champion Machinery's commitment to improving mutual understanding and providing exceptional service. As a result, Champion Machinery's footprints have been established in various regions, including Asia, Europe, Oceania, North and South America, Africa, and the Middle East.Champion Machinery's main product line includes a comprehensive range of industrial machinery, with the PVC Sheet Cutting Machine serving as a standout solution for efficient and precise cutting processes. Built with advanced technology and high-quality materials, the PVC Sheet Cutting Machine is designed to enhance the precision and accuracy of cutting PVC sheets, saving time and effort for businesses in the manufacturing, packaging, and signage industries.The PVC Sheet Cutting Machine is equipped with high-tech features that enable it to accurately cut PVC sheets to the desired size and shape, making it an essential tool for production lines. Furthermore, the machine's durable construction ensures optimal performance and longevity, making it a reliable investment for businesses seeking to streamline their cutting processes.As a testament to Champion Machinery's commitment to quality and excellence, the company offers top-notch after-sales service, providing customers with technical support and maintenance assistance to ensure that their cutting machines remain in perfect condition. This dedication to customer satisfaction sets Champion Machinery apart as a trusted partner for businesses seeking high-quality cutting solutions.The PVC Sheet Cutting Machine is designed for optimal cutting performance, with advanced features such as automatic feeding, high-speed cutting, and accurate positioning. Moreover, the machine is easy to operate and requires minimal maintenance, making it a cost-effective investment for businesses of all sizes.In addition to its technological capabilities, the PVC Sheet Cutting Machine is equipped with safety features to ensure the operator's protection during the cutting process, making it suitable for use in a wide range of industries, including packaging, printing, and signage. Its versatility and flexibility enable it to handle a variety of materials, including PVC, foam board, acrylic, and more.Customer testimonials affirm the effectiveness and efficiency of the PVC Sheet Cutting Machine, with users praising its ease of use, durability, and precision cutting capabilities. Ms. Carlen Shu, a satisfied customer, attests to the machine's essential role in streamlining the cutting process for PVC sheets, while Ms. Angela Her acknowledges the advanced technology and sturdiness of the machine, making it a highly recommended cutting solution for the PVC industry.With its dedication to expanding its global presence and providing high-quality industrial machinery, Champion Machinery is poised to continue delivering cutting-edge solutions to customers worldwide. By offering top-quality products and exceptional service, Champion Machinery has solidified its position as a trusted partner for businesses seeking efficient and precise cutting solutions for their production needs.For businesses looking for reliable PVC sheet cutting machines that guarantee high precision and efficiency, Champion Machinery's PVC Sheet Cutting Machine is the perfect solution. Contact Champion Machinery today to learn more about their products and how they can benefit your business.
High-Quality PVC Plastic Welding Machine Manufacturer and Supplier in China - Top Quality from Factory
Champion Machinery, a leading manufacturer, supplier, and factory of welding machines, has recently introduced their top-quality PVC plastic welding machine to the international market. With a global strategy in place, Champion is focused on expanding its presence in international markets and establishing a strong agent network to promote and localize their brand. Their efforts have resulted in a significant presence across Asia, Europe, Oceania, North and South America, Africa, and the Middle East.The PVC plastic welding machine offered by Champion Machinery is designed with precision and technical expertise, ensuring exceptional performance, reliability, and efficiency. It is an ideal tool for welding and joining PVC plastic materials and is suitable for a variety of applications, ranging from small DIY projects to industrial tasks. The machine is equipped with the latest technology, including a high-performance heating system that ensures consistent and even heating of the welding material, resulting in strong and durable welds that are resistant to wear and tear.One of the key features of Champion's PVC plastic welding machine is its user-friendly design, making it easy to operate for users of all skill levels. The machine's intuitive controls and ergonomic grip ensure convenience and ease of use, while its lightweight and portable design allow for easy transport and maneuverability, even in confined workspaces. Additionally, the machine is built with safety features, such as a built-in protection system that prevents overheating and short circuits, offering users a safe and worry-free welding experience.Champion Machinery takes pride in ensuring that their products meet the highest quality standards, and their commitment to customer satisfaction is evident in the design and performance of their PVC plastic welding machine. Their dedication to innovation in welding technology has earned them a strong reputation in the industry, making them a trusted choice for professionals and DIY enthusiasts alike.In addition to the PVC plastic welding machine, Champion Machinery offers a wide range of other products, including Vacuum forming, Recycling plastic, Sheet film Line, Blow/injection molding machine, EPE foam machine, Hydraulic cutting machine, and Air compressor/Screw compressor/Chiller/Hopper dryer/Crusher/Mixer/Auto loader all in 1 intelligent integrated system solutions for Material Feeding, Air Supply, Water Supply, and Power Supply. This diverse product system allows Champion to efficiently meet customized demands based on their technical strength and supply chain advantages.Customers can rely on Champion Machinery for top-quality products and services, backed by their years of experience and expertise in the industry. Their dedication to exploring international markets and establishing a strong global presence speaks volumes about their commitment to serving customers worldwide. By paying visits to customers overseas for face-to-face communication, Champion Machinery strives to improve mutual understanding and provide exceptional service to customers in every corner of the globe.Overall, Champion Machinery's PVC plastic welding machine is a testament to their dedication to delivering top-quality products that meet the needs of professionals and DIY enthusiasts alike. With their global presence and commitment to excellence, customers can trust Champion Machinery to provide reliable performance and exceptional results in all of their welding needs.In conclusion, Champion Machinery's PVC plastic welding machine is a highly efficient, reliable, and versatile tool that offers a cost-effective and convenient solution for all welding needs. Whether it's for small DIY projects or industrial tasks, the PVC plastic welding machine is designed to deliver consistent results with ease of use, safety features, and durable construction. Champion Machinery's dedication to customer satisfaction and their extensive range of products make them a trusted and reputable choice for customers worldwide.
Molding Machine Manufacturer, Supplier, Factory in China
Champion Machinery Expands its Global Reach with High-Quality Molding MachinesAs part of its global expansion strategy, Champion Machinery has been actively exploring international markets and establishing a robust global agent network. The company has been dedicated to promoting its brand and localizing its products to better serve customers worldwide. With a strong presence in Asia, Europe, Oceania, North and South America, Africa, and the Middle East, Champion Machinery has proven its commitment to delivering high-quality equipment and exceptional service on a global scale.One of Champion Machinery's standout products is the cutting-edge molding machine, a testament to the company's dedication to technological advancement and customer satisfaction. The molding machine series, including Vacuum forming, Recycling plastic, Sheet film Line, Blow/injection molding machine, EPE foam machine, Hydraulic cutting machine, Air compressor/Screw compressor/Chiller/Hopper dryer/Crusher/Mixer/Auto loader, offers an all-in-one intelligent integrated system solution for Material Feeding, Air Supply, Water Supply, and Power Supply. This comprehensive product range is designed to efficiently meet customized demands with technical expertise and robust supply chain advantages.The Vishwakarma Molding Machine, a key offering in Champion Machinery's product lineup, has been gaining recognition for its exceptional performance, reliability, and advanced features. Designed to meet a wide range of manufacturing applications, the Vishwakarma Molding Machine is suitable for various molding projects, including plastic injection molding, blow molding, and compression molding. With its high-speed capabilities, advanced automation, and user-friendly interface, this state-of-the-art machine is the ideal solution for manufacturers looking to streamline operations and boost productivity.Customer testimonials further demonstrate the excellence of Champion Machinery's molding machines. Ms. Carlen Shu, a satisfied user, praised the machine for its reliability, user-friendly design, and ability to produce high-quality molds for diverse applications. She emphasized the machine's advanced technology and durability, making it a valuable investment for businesses of all sizes. Similarly, Ms. Angela Her highlighted the performance and durability of Champion Machinery's molding machines, noting their advanced features, intelligent controls, and eco-friendly, energy-efficient design, making them ideal for both small and large-scale production.Champion Machinery's commitment to providing high-quality equipment extends beyond product excellence. The company places great emphasis on building strong customer relationships and providing exceptional service. Through face-to-face communication and visits to customers overseas, Champion Machinery has been able to improve mutual understanding and enhance its service delivery to customers worldwide. This personalized approach has contributed to the company's success in establishing a strong foothold in international markets and earning the trust and loyalty of customers globally.In conclusion, Champion Machinery's dedication to global expansion, technological innovation, and customer satisfaction has positioned the company as a leading provider of high-quality molding machines and intelligent integrated system solutions. With a strong global presence and a focus on building lasting customer relationships, Champion Machinery continues to set the standard for excellence in the manufacturing industry. For manufacturers seeking reliable, efficient, and advanced molding solutions, Champion Machinery remains the top choice.
Manufacturer and Supplier for Ps Foam Sheet Extrusion Line in China
GUANGDONG CHAMPION AUTOMATION TECHNOLOGY CO., LTD, a leading manufacturer and supplier of plastic machinery and equipment, has been actively expanding its international presence and delivering high-quality, efficient, and customized solutions to customers worldwide. With a strong global agent network, technical strength, and supply chain advantages, Champion Machinery is committed to meeting the unique needs of customers in various industries, including packaging, insulation, construction, and more.Champion Machinery’s main product range, known as the “Many” Product System, includes six series of products: Vacuum forming, Recycling plastic, Sheet film Line, Blow/injection molding machine, EPE foam machine, and Hydraulic cutting machine. In addition, the company offers a range of supporting equipment, such as air compressors, screw compressors, chillers, hopper dryers, crushers, and mixers. These products can be seamlessly integrated into a single, intelligent, and efficient system, providing customers with a comprehensive solution for material feeding, air supply, water supply, and power supply.With a strong focus on innovation and R&D, Champion Machinery has established itself as a Guangdong Hi-Tech Enterprise and an A-Level Taxpayer for five consecutive years. The company has also been appointed as the “Jiangmen Engineering R&D Center” and an “Industry-University-Research Cooperation Base,” demonstrating its commitment to continuous improvement and development.One of Champion Machinery’s core strengths lies in its global strategy and exploration of international markets. Since the early 2000s, the company has been actively participating in international exhibitions and conferences, establishing overseas offices and agents, and promoting its brand in various countries. The global agent network covers Asia, Europe, Oceania, North and South America, Africa, and the Middle East, ensuring comprehensive coverage and support capabilities for customers worldwide.To further enhance communication and service with overseas customers, Champion Machinery has been sending its sales and technical teams to visit customers in different countries regularly. This face-to-face communication allows the company to provide technical support, after-sales service, and build mutual understanding and trust with customers, ultimately fostering long-term cooperation and partnerships.In terms of technical strength, Champion Machinery boasts a team of over 50 skilled engineers and technicians who continuously follow market trends and customer needs, while keeping pace with advanced technology in the industry. The company is committed to providing customers with high-quality, efficient, and customized machinery and equipment solutions that meet their specific production requirements.Furthermore, Champion Machinery has established strategic partnerships with universities and research institutes to enhance its technical strength and development capacity. This collaboration allows the company to independently develop and design new machinery and equipment, meeting the unique needs of different customers in various industries.The company has also focused on building a robust supply chain system, working with reliable and efficient suppliers to ensure the quality and stable supply of raw materials and accessories. In addition, Champion Machinery has established an excellent logistics and distribution system, which enables it to efficiently deliver machinery and equipment to customers worldwide.Moreover, Champion Machinery is dedicated to meeting the personalized needs of customers in different industries. The company provides comprehensive solutions tailored to the customer's requirements, production capacity, plant size, and other factors. This personalized approach ensures that the machinery and equipment not only meet the customer's production needs but also improve production efficiency and reduce operation costs.In addition to providing high-quality machinery and equipment, Champion Machinery also offers a range of after-sales services, including technical guidance, equipment maintenance, and spare parts supply. The company has a team of professional and highly trained service engineers who can respond quickly to customer requests and provide timely and effective support.Champion Machinery's commitment to innovation, quality, and service reflects its ambition to become a world-renowned supplier in the plastic machinery and equipment industry. With its comprehensive product range, global presence, technical expertise, and customer-centric approach, the company is well-positioned to meet the evolving needs of customers worldwide and contribute to the growth and success of various industries.
Innovative Injection Molding Machines: A Technology Revolutionizing Industries
Title: Groundbreaking Injection Molding Machine Revolutionizes Manufacturing Processes Introduction:In an era where product innovation and efficiency are critical to success, cutting-edge technology plays an instrumental role. A leading pioneer in the manufacturing industry, [Company Name], has recently unveiled a groundbreaking Injection Molding Machine that is set to redefine manufacturing standards worldwide. This visionary machine, developed after years of extensive research and development, promises to revolutionize the injection molding process, thereby amplifying productivity while ensuring superior quality output.Body:1. Overview of the Injection Molding Machine: The revolutionary Injection Molding Machine by [Company Name] boasts breakthrough features that will propel the manufacturing industry into a new realm of possibilities. Unlike conventional machines, this state-of-the-art equipment combines advanced technology, precision engineering, and unparalleled control systems to deliver exceptional outcomes. Its user-friendly interface coupled with intelligent automation simplifies intricate production tasks and empowers manufacturers to take their operations to unparalleled heights of efficiency and reliability.2. Key Features and Benefits: a) Enhanced Precision and Reproducibility: By harnessing cutting-edge technologies, this Injection Molding Machine ensures precise control over every minute detail of the molding process. From temperature and pressure to speed and flow rates, manufacturers can achieve unparalleled accuracy, leading to consistently high-quality end products. b) Improved Efficiency and Productivity: The incorporation of innovative automation mechanisms into the machine's design drastically reduces production time and minimizes the need for manual labor-intensive tasks. Manufacturers can now witness a substantial increase in output while optimizing costs and resources efficiently. c) Versatility and Adaptability: [Company Name]'s machine is designed to cater to a wide range of materials, making it ideal for diverse industries. Be it plastics, rubbers, or even metal alloys, this injection molding solution ensures seamless adaptation to various manufacturing requirements, enabling businesses to explore new avenues of production. d) Eco-Friendly Design: In line with today's sustainable practices, this Injection Molding Machine leverages energy-efficient technologies, reducing the overall carbon footprint without compromising on performance. This eco-friendly approach aligns with the global focus on responsible manufacturing practices, attracting environmentally conscious businesses looking to make a positive impact.3. Competitive Edge: With relentless research and development efforts, [Company Name] has managed to outshine its competitors by introducing several unique features within the injection molding industry. Cutting-edge innovations like real-time monitoring, predictive maintenance capabilities, and intelligent quality control systems set this machine apart. By constantly staying ahead of the curve, [Company Name] emphasizes its commitment to providing manufacturers with pioneering solutions that boost productivity, reduce costs, and elevate product quality.4. Industry-wide Applications: This Injection Molding Machine's versatility extends its applications far beyond traditional manufacturing sectors. From automotive parts, appliances, and electronics to medical equipment, packaging materials, and consumer goods, this revolutionary machine finds its utilization in various industries worldwide. Its adaptability and precision make it a sought-after solution for any business aiming to streamline their manufacturing processes.5. Future Prospects: [Company Name] believes that this unprecedented Injection Molding Machine is only the beginning of a new manufacturing era. Its continuous efforts to enhance operational efficiency, as well as invest in research and development, lay the foundation for breakthrough advancements that will fuel tomorrow's industries. The company's vision is to empower manufacturers globally with innovative solutions that push the boundaries of what's possible in injection molding.Conclusion:[Company Name]'s remarkable Injection Molding Machine represents a landmark achievement in the manufacturing industry. By combining cutting-edge technology, superior engineering, and visionary thinking, this machine epitomizes the company's commitment to revolutionizing manufacturing processes worldwide. With enhanced precision, increased productivity, adaptability, and an eco-friendly approach, this machine ushers in a new era of possibilities for manufacturers across various sectors. Through constant innovation and an unwavering dedication to excellence, [Company Name] cements its position as a global leader driving the future of injection molding technology.