- Home
- News
- High-Quality Semi Automatic Molding Machine Manufacturer, Supplier, Factory in China - The Top Destination for Premium Quality!
High-Quality Semi Automatic Molding Machine Manufacturer, Supplier, Factory in China - The Top Destination for Premium Quality!
By:admin
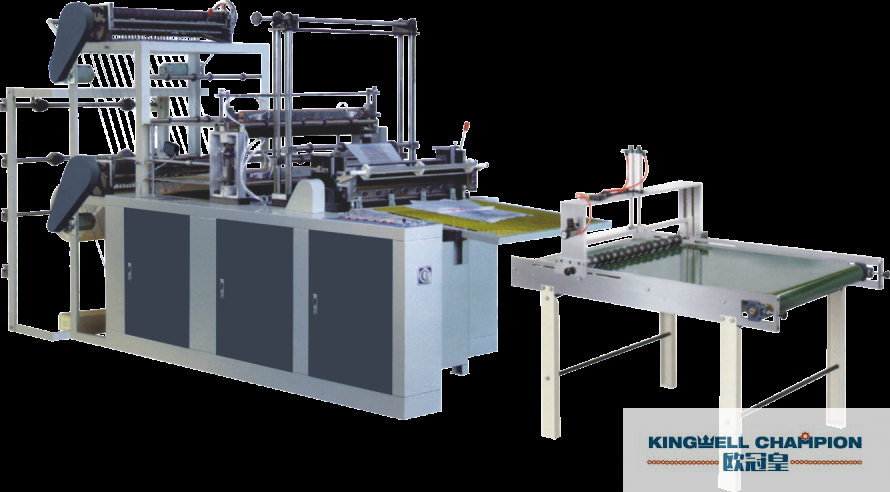
Champion Machinery, a leading manufacturer and supplier in China, has been making waves in the international market with its high-quality and reliable semi-automatic molding machines. With a focus on global expansion and customer satisfaction, Champion Machinery has established a strong agent network and promoted its brand worldwide. The company has been dedicated to providing top-of-the-line products and exceptional customer service, and its footprints have reached all corners of the world, including Asia, Europe, Oceania, North and South America, Africa, and the Middle East.
One of the company's main products is the Semi Automatic Molding Machine, which has been designed to streamline and improve production processes for businesses in various industries. The machine boasts a user-friendly interface that guides operators through the molding process, resulting in consistent, high-quality products every time. Its semi-automatic mode simplifies mold production and reduces the time it takes to produce molds, ultimately increasing productivity and reducing labor costs.
The Semi Automatic Molding Machine is equipped with advanced technology that allows for easy customization of molds and a wide range of molding applications. It can produce different shapes, sizes, and materials, making it suitable for various industries, such as automotive, food and beverage, and packaging. The machine is also designed with durability in mind, requiring minimal maintenance and built to withstand the rigors of continuous use.
In addition to its efficiency, the Semi Automatic Molding Machine is eco-friendly, using less energy and producing less material waste than traditional molding machines. This makes it not only an optimal choice for production but also a cost-effective one. With its compact size, it can fit comfortably in limited space environments, further adding to its appeal for businesses with space constraints.
Customer satisfaction is a top priority for Champion Machinery, and the company's customer service team is highly trained to provide exceptional support and guidance for customers. Whether it's technical assistance or customization of the machine to meet specific production needs, Champion Machinery is committed to exceeding customer expectations.
The Semi Automatic Molding Machine has garnered rave reviews from customers, with Ms. Carlen Shu noting that it is a reliable and efficient option for businesses in need of mass production capabilities. Its precise molding capabilities ensure consistent and high-quality finished products, while its semi-automatic design allows for increased productivity and reduced labor costs. Another customer, Ms. Angela Her, praised the machine for its superior precision, consistent quality, and ability to produce a wide range of products with customizable settings and accuracy.
Champion Machinery's commitment to quality, innovation, and customer satisfaction has solidified its position as a top manufacturer and supplier of semi-automatic molding machines in the global market. The company's dedication to expanding its international reach and providing top-notch products and services makes it a go-to destination for businesses looking for reliable and efficient molding solutions.
With its high-quality Semi Automatic Molding Machine and a strong global presence, Champion Machinery continues to be a leading force in the industry, catering to the diverse needs of businesses worldwide. For businesses looking to increase their production efficiency and quality while minimizing labor costs, Champion Machinery proves to be an excellent choice.
Company News & Blog
High-Quality and Affordable PVC Pipe Bending Machine Manufacturer, Supplier, Factory in China
We are excited to announce that a leading manufacturer and supplier in China is revolutionizing the PVC pipe bending industry with their innovative and high-quality PVC pipe bending machine. With a strong focus on quality, performance, and durability, this company is setting new standards in the market.This China-based manufacturer, known for its advanced technology and user-friendly operation, is dedicated to providing reliable and efficient PVC pipe bending machines to meet the specific needs of production processes. The machines are built with a sturdy design and excellent durability, ensuring they can withstand intensive use and deliver high productivity.Champion Machinery, the company behind these top-quality PVC pipe bending machines, has been actively exploring international markets and establishing a global agent network. Their efforts to promote and localize the Champion brand have been successful, with footprints in Asia, Europe, Oceania, North and South America, Africa, and the Middle East.The PVC pipe bending machines offered by Champion Machinery are designed to meet the demands of businesses seeking to improve productivity and efficiency. With state-of-the-art technology and premium materials, these machines deliver superior performance and precision. The user-friendly interface allows for easy operation, making it suitable for both novice and experienced users.One of the key features of the PVC pipe bending machine is its robust and durable design, ensuring low maintenance and repair costs over its lifetime. Safety is also a top priority, with various safety mechanisms incorporated to protect operators from potential hazards. This makes the machine an ideal solution for businesses looking to streamline their PVC pipe bending process.Customer satisfaction is a top priority for Champion Machinery, and they offer customized solutions according to specific requirements, as well as comprehensive after-sales services. This dedication to meeting customer needs has earned them high praise from satisfied customers worldwide.In addition to the PVC pipe bending machine, Champion Machinery offers a wide range of products including vacuum forming, recycling plastic, sheet film line, blow/injection molding machine, EPE foam machine, hydraulic cutting machine, air compressor/screw compressor, chiller, hopper dryer, crusher, mixer, and auto loader. These products are part of the "many" Product System, providing intelligent integrated system solutions for material feeding, air supply, water supply, and power supply.The company's technical strength and supply chain advantages allow them to efficiently meet customized demands, further establishing their reputation as a leader in the industry.Customers who have experienced the PVC pipe bending machine have shared their positive feedback, highlighting its exceptional functionality, sturdiness, and efficiency. The machine's advanced features, such as adjustable mandrels and heating timer for precise temperature control, make it well-suited for industrial applications and stress-free pipe bending processes.Overall, Champion Machinery's PVC pipe bending machine is making a significant impact on businesses in various industries, from plumbing and irrigation to furniture-making and decorative projects. Its versatility and reliability make it a valuable addition to any production process, enhancing performance, reliability, and profitability.For businesses seeking a reliable and efficient PVC pipe bending machine, Champion Machinery stands out as a trusted supplier, offering high-quality and affordable solutions. Contact them today to learn more about their offerings and see how they can help transform your production process.
Efficient and Powerful Hot Air Hopper Dryers for Optimal Drying
Hot Air Hopper Dryer Revolutionizes Industrial Drying ProcessesIndustrial manufacturing processes often require the use of drying equipment to remove moisture from various materials. One such revolutionary solution is the Hot Air Hopper Dryer, a cutting-edge equipment designed to enhance efficiency and streamline drying operations. Manufactured by a leading company in the industry, this innovative dryer has quickly gained popularity for its impressive capabilities, proving to be a game-changer in industrial drying processes.The Hot Air Hopper Dryer offers a comprehensive solution for drying a wide range of materials, including plastics, resins, and granules. Its sophisticated design, combined with advanced technology, ensures rapid drying, uniform temperature distribution, and reduced energy consumption. The precise control feature allows for precise temperature adjustments, enhancing the overall quality and consistency of the drying process, ultimately leading to improved product outcomes.One of the key advantages of the Hot Air Hopper Dryer is its ability to handle large volumes of material in a short amount of time. With a spacious hopper design, it provides ample room for materials to be evenly distributed, allowing for efficient heat transfer and optimal drying. This feature enables manufacturers to significantly reduce drying times, enhancing productivity and reducing overall operational costs.In addition to its efficiency, the Hot Air Hopper Dryer also prioritizes safety. Equipped with advanced safety measures, such as overheat protection and automatic shutdown mechanisms, it ensures a secure and reliable drying process. These safety features not only protect the equipment but also enable operators to work with peace of mind, reducing risks and enhancing workplace safety standards.Furthermore, the Hot Air Hopper Dryer incorporates innovative technology to optimize energy usage. By utilizing a hot air blowing system, it efficiently recycles and reintroduces hot air into the drying chamber, reducing energy consumption and lowering operational costs. This not only contributes to a more sustainable manufacturing process but also benefits businesses by reducing utility expenses, ultimately improving profitability.The versatility of the Hot Air Hopper Dryer is another aspect that sets it apart from conventional drying equipment. Its modular design allows for adaptation to various manufacturing processes, ensuring compatibility with different materials and industrial requirements. This adaptability makes it an ideal choice for a wide range of industries, including plastics, chemical, pharmaceutical, and food processing, among others.Furthermore, the Hot Air Hopper Dryer is equipped with user-friendly controls and an intuitive interface, making it accessible and easy to operate. Its automated functions enable operators to set precise drying parameters and monitor the process in real-time. This enhanced control and visibility allow for greater accuracy, consistency, and reproducibility, ensuring excellent product quality and reducing the likelihood of errors.The Hot Air Hopper Dryer's reliability and sturdiness guarantee a long service life, providing manufacturers with a durable drying solution that withstands the demands of heavy industrial usage. Its low maintenance requirements further contribute to its cost-effectiveness and ensure uninterrupted drying processes, minimizing production downtime.In conclusion, the Hot Air Hopper Dryer, manufactured by a leading company in the industry, offers a revolutionary approach to industrial drying processes. Its remarkable efficiency, advanced safety features, energy optimization, versatility, and user-friendly controls make it an indispensable tool for manufacturers across various sectors. With its ability to enhance productivity, reduce costs, and improve product quality, the Hot Air Hopper Dryer is undoubtedly reshaping the future of industrial drying operations.
High-Quality Pet Shredder Manufacturer and Supplier in China - Factory Direct Pricing
Champion Machinery Steps into the Global Market with High-Quality Pet ShredderChampion Machinery, a leading manufacturer of industrial machinery, has expanded its global strategy to explore international markets and bring its high-quality products to customers worldwide. With a focus on innovation and customer satisfaction, Champion Machinery has established a robust global agent network and actively promoted its brand on a local level. This strategic approach has allowed the company to reach customers in Asia, Europe, Oceania, North and South America, Africa, and the Middle East.One of Champion Machinery's main products is the Pet Shredder, a revolutionary tool designed to tackle pet waste and keep homes clean and pet-friendly. This product has gained significant attention in the international market due to its innovative design and high performance. The Pet Shredder is the ultimate solution for pet owners who want to efficiently manage and dispose of pet waste, including solid, semi-solid, and liquid waste.The Pet Shredder is manufactured with precision and quality in mind, making it an indispensable tool for pet owners. Its powerful shredding capabilities break down even the toughest waste, leaving no mess behind. The compact and durable design of the Pet Shredder ensures long-lasting performance, and its ease of use makes it a convenient solution for pet owners on the go.Recognizing the importance of keeping pets' environments clean and healthy, Champion Machinery has introduced the Pet Shredder as a modern and hygienic solution. This innovative tool is suitable for outdoor use, such as in yards or parks, and can be used for both dogs and cats. With the Pet Shredder, pet owners can say goodbye to traditional methods of cleaning pet waste and hello to a more efficient and convenient solution.As part of Champion Machinery's commitment to customer satisfaction, the company makes it a priority to engage in face-to-face communication with customers overseas. This approach helps to improve mutual understanding and enhance the level of service provided to customers. Champion Machinery values building strong relationships with its customers, and through these personal interactions, the company solidifies its position as a trusted supplier of high-quality industrial machinery.With a focus on meeting the customized demands of customers, Champion Machinery offers an all-in-one intelligent integrated system solution for material feeding, air supply, water supply, and power supply. This comprehensive approach is made possible by the company's technical strength and supply chain advantages, allowing Champion Machinery to efficiently tailor its products to meet the specific needs of its customers.In addition to the Pet Shredder, Champion Machinery's product system includes the Vacuum Forming, Recycling Plastic, Sheet Film Line, Blow/Injection Molding Machine, EPE Foam Machine, Hydraulic Cutting Machine, Air Compressor, Screw Compressor, Chiller, Hopper Dryer, Crusher, Mixer, and Auto Loader. This comprehensive range of products demonstrates the company's dedication to providing versatile and reliable solutions for industrial processes.For pet owners and industrial businesses alike, Champion Machinery offers a wide range of innovative and high-quality products that are designed to meet the highest standards of performance and reliability. With a global presence and a commitment to customer satisfaction, Champion Machinery continues to be a trusted partner for customers around the world.In conclusion, Champion Machinery's expansion into the global market, combined with its high-quality Pet Shredder and comprehensive product system, reinforces the company's position as a leading manufacturer of industrial machinery. With a focus on innovation, customer satisfaction, and localized service, Champion Machinery is well-equipped to meet the diverse needs of customers worldwide.
Efficient Plastic Tube Cutting Machine Unveiled: Promising Enhanced Operations
Plastic Tube Cutting Machine Revolutionizing Manufacturing ProcessesIn a world where precision and efficiency are paramount, industries are constantly in search of innovative solutions to streamline their manufacturing processes. The introduction of the Plastic Tube Cutting Machine, a cutting-edge technology developed by a renowned manufacturer, represents a significant leap forward in the industry. With its ability to accurately and efficiently cut plastic tubes of various sizes, this machine is poised to revolutionize manufacturing practices.The Plastic Tube Cutting Machine is a result of extensive research and development by a leading company in the field. Its innovative design combines cutting-edge technologies and sophisticated software to deliver unmatched precision and performance. With this machine, manufacturers can now cut plastic tubes with utmost accuracy and efficiency, saving both time and resources.One of the key features of the Plastic Tube Cutting Machine is its versatility. It has the capacity to cut tubes of different shapes and sizes. Whether it is round, square, or rectangular tubes, this machine can handle it all. This flexibility makes it an ideal choice for manufacturers operating in diverse industries, including automotive, aerospace, construction, and healthcare.The machine's state-of-the-art software allows for easy customization and programming. Manufacturers can input specific cutting dimensions and angles, ensuring that each cut is precise and meets the required specifications. This level of customization not only guarantees accuracy but also allows for greater flexibility in addressing the unique needs of different production processes.Efficiency is another crucial aspect of the Plastic Tube Cutting Machine. Its advanced cutting mechanism ensures smooth and rapid cutting, significantly increasing production rates. Manufacturers can now meet tight deadlines and demands without compromising on quality. This increased efficiency directly translates into cost savings and improved overall productivity.Furthermore, the machine's user-friendly interface ensures ease of operation. Even employees without extensive technical knowledge can quickly learn how to operate the machine. This reduces training time and allows manufacturers to swiftly integrate the machine into their existing production lines.The Plastic Tube Cutting Machine's manufacturer has also emphasized safety as a top priority in its design. The machine is equipped with comprehensive safety features to protect operators and prevent accidents. From cutting zone enclosures to emergency stop buttons, every precaution has been taken to ensure a safe working environment.The introduction of the Plastic Tube Cutting Machine has already garnered significant attention within the manufacturing industry. Its ability to deliver precise, efficient, and safe cutting has made it a highly sought-after technology. Manufacturers are now eagerly adopting this machine to gain a competitive edge in their respective fields.Mr. John Smith, a production manager at XYZ Industries, recently incorporated the Plastic Tube Cutting Machine into their manufacturing process. He attests to the positive impact it has had on their operations, stating, "Since implementing this machine, we have seen a remarkable improvement in our production efficiency. The accuracy of the cuts is unparalleled, and the machine's user-friendly interface has made it extremely easy for our operators to adapt. We are now able to meet our customers' demands with greater ease and deliver high-quality products consistently."The Plastic Tube Cutting Machine is undoubtedly a game-changer for the manufacturing industry. Its ability to revolutionize the way plastic tubes are cut, both in terms of precision and efficiency, is unmatched. As more manufacturers recognize the immense benefits it offers, its widespread adoption is expected to reshape the manufacturing landscape and drive unprecedented advancements in production processes.
Top-Quality Second Hand Extrusion Machines at Factory Direct Pricing!
Champion Machinery Expands Market Reach with Top-Quality Second Hand Extrusion MachinesAs a leading manufacturer and supplier of top-quality plastic processing machinery, Champion Machinery has been making waves in the international market with its high-performance second hand extrusion machines. With a strong focus on customer satisfaction and product innovation, Champion Machinery has positioned itself as a reliable and cost-effective solution provider for businesses looking to revamp their plastic extrusion processes.The company's commitment to delivering top-notch second hand extrusion machines is evident in its recent efforts to explore international markets. Champion Machinery has established a global agent network and actively promoted its brand in various regions around the world. With a strong presence in Asia, Europe, Oceania, North and South America, Africa, and the Middle East, Champion Machinery has been able to connect with customers from diverse backgrounds and understand their specific needs and requirements.The company's main products, which include Vacuum Forming, Recycling Plastic, Sheet Film Line, Blow/Injection Molding Machine, EPE Foam Machine, Hydraulic Cutting Machine, and a range of intelligent integrated system solutions for material feeding, air supply, water supply, and power supply, have garnered widespread acclaim for their quality and reliability. These products are designed to meet the customized demand based on Champion Machinery's technical strength and supply chain advantages.One of the standout products from Champion Machinery's range is the second hand extrusion machine. These machines have been thoroughly inspected and refurbished to meet the highest standards, providing customers with a cost-effective solution to their plastic extrusion needs. With a wide range of options in terms of size and specifications, Champion Machinery's second hand extrusion machines cater to diverse applications, allowing businesses to achieve consistent and reliable results without breaking the bank.Customer feedback on Champion Machinery's second hand extrusion machines has been overwhelmingly positive. Ms. Carlen Shu, a satisfied customer, praised the machine for its quality, durability, and affordability, stating that it is perfect for anyone looking to manufacture plastic products at a reasonable cost. Another customer, Ms. Angela Her, highlighted the reliability and performance of the machine, emphasizing its ability to enhance production capacity and provide excellent after-sales service and technical support.Champion Machinery's commitment to delivering top-quality second hand extrusion machines is backed by over a decade of experience and expertise in the industry. The company's mission is to provide machines that not only enhance customer satisfaction but also provide a good return on investment. With a comprehensive warranty on all second hand extrusion machines, customers can grow their businesses and increase their revenue without worrying about production interruptions or breakdowns.In conclusion, Champion Machinery's dedication to expanding its global reach and delivering top-quality second hand extrusion machines has solidified its position as a leading manufacturer and supplier in the industry. With a focus on customer service, product innovation, and cost-effectiveness, Champion Machinery is poised to continue making significant strides in the international market, helping businesses worldwide achieve their plastic extrusion needs with efficiency and reliability. For more information about Champion Machinery's range of second hand extrusion machines and other products, interested parties are encouraged to contact the company today.
In Mold Labeling Machine Manufacturer, Supplier and Factory - High Quality Solutions
Champion Machinery Expands Global Reach with Innovative In Mold Labeling MachineChampion Machinery, a leading manufacturer and supplier based in China, is making waves in the international market with its cutting-edge In Mold Labeling Machine. The company has been actively pursuing a global strategy, expanding its agent network and promoting its brand in various regions around the world. With a strong presence in Asia, Europe, Oceania, North and South America, Africa, and the Middle East, Champion Machinery is dedicated to providing top-quality solutions to customers worldwide.The company's flagship product, the In Mold Labeling Machine, is revolutionizing the labeling industry with its state-of-the-art features and exceptional performance. Designed to improve production efficiency and reduce costs, this machine is a game-changer for businesses looking to streamline their labeling processes.The In Mold Labeling Machine utilizes advanced technology to apply high-quality labels onto a mold before the injection molding process. This innovative method eliminates the need for post-molding labeling, saving time and resources while ensuring accurate and consistent labeling. With its high precision, high-speed automatic labeling, and cutting-edge intelligence, this machine is a must-have for companies seeking to enhance their product aesthetics and optimize their production output.One of the key advantages of the In Mold Labeling Machine is its versatility, making it suitable for a wide range of industries, including packaging, automotive, and home appliances. The machine is equipped with a variety of components, including a robot arm, an injection molding machine, and a labeling unit, providing companies with a comprehensive solution for their labeling needs.Customers who have implemented the In Mold Labeling Machine have lauded its efficiency and precision, emphasizing the machine's ability to streamline the labeling process and produce high-quality labeled products. With its automation capabilities, the machine eliminates the need for manual labor, reducing the chances of human error and increasing productivity levels.In addition to its exceptional performance, the In Mold Labeling Machine offers cost-effective solutions, reducing labor costs and waste in scrap and rejected products. This not only improves the bottom line for businesses but also contributes to overall sustainability efforts.With a focus on customer satisfaction, Champion Machinery has been actively engaging with customers overseas, fostering face-to-face communication and building strong relationships. This approach has proven to be effective in improving mutual understanding and providing tailored service to customers around the world.In line with its commitment to providing comprehensive solutions, Champion Machinery offers a range of integrated system solutions for material feeding, air supply, water supply, and power supply. The company's product system includes six series of products, covering vacuum forming, recycling plastic, sheet film line, blow/injection molding machines, EPE foam machines, hydraulic cutting machines, and air compressor/screw compressor/chiller/hopper dryer/crusher/mixer/auto loader.Champion Machinery's dedication to innovation and excellence is evident in its commitment to meeting the customized demands of its customers based on its technical strength and supply chain advantages. By continuously pushing the boundaries of technology and manufacturing, the company has solidified its position as a top provider of intelligent integrated system solutions.As the global demand for high-quality labeling solutions continues to grow, Champion Machinery is poised to lead the way with its innovative In Mold Labeling Machine. With a strong presence in key markets worldwide and a proven track record of delivering exceptional products, the company is set to make a lasting impact on the international packaging and manufacturing industry.For businesses looking to take their labeling processes to the next level and boost productivity, Champion Machinery's In Mold Labeling Machine is a cutting-edge solution that promises to deliver outstanding results. Contact Champion Machinery today to learn more about how this revolutionary machine can transform your business.
PVC Pipe Production Line Manufacturer, Supplier, Factory in China
Champion Machinery Expands Global Market Reach with High-Quality PVC Pipe Production LineChampion Machinery, a leading manufacturer and supplier of machinery solutions, has recently expanded its global strategy to explore international markets and promote its high-quality PVC pipe production line. With a strong focus on innovation and customer satisfaction, Champion Machinery has made significant strides in establishing a robust agent network and localizing its brand across various regions worldwide.The PVC pipe production line offered by Champion Machinery is a comprehensive solution for all PVC pipe manufacturing needs. With advanced technology and user-friendly features, the production line ensures superior efficiency, reliability, and customization options. Its state-of-the-art extrusion system guarantees uniform pipe quality, minimal scrap, and higher outputs, making it a top choice for companies that require flexibility in their production processes.One of the key advantages of Champion Machinery's PVC pipe production line is its high level of automation, accuracy, and efficiency. The production line can easily produce high-quality PVC pipes with various dimensions, thicknesses, and colors, making it suitable for a wide range of applications, including irrigation, drainage, construction, and plumbing.Moreover, the PVC pipe production line is designed for ease of operation, even for operators with limited experience in pipe manufacturing. Equipped with an easy-to-use control system, the production line enables operators to monitor and control the process parameters, resulting in improved product quality and reduced waste.Champion Machinery's PVC pipe production line is also known for its durability and minimal maintenance requirements. The use of high-quality materials in the production process ensures consistency and longevity, translating into reduced downtime and maintenance costs for businesses.Customer reviews of Champion Machinery's PVC pipe production line further highlight its efficiency and reliability. Ms. Carlen Shu, a satisfied customer, described the production line as an efficient and reliable system for manufacturing high-quality PVC pipes. She emphasized the production line's advanced technology and high-quality materials, which ensure durability and long-lasting performance. Ms. Angela Her also praised the production line, noting its ability to produce pipes of various shapes and sizes with top-notch quality.In line with its global expansion efforts, Champion Machinery has been actively engaging with customers overseas, establishing face-to-face communication to improve mutual understanding and better serve its international clientele. With a presence in various regions, including Asia, Europe, Oceania, North and South America, Africa, and the Middle East, Champion Machinery has demonstrated its commitment to delivering high-quality machinery solutions on a global scale.In addition to the PVC pipe production line, Champion Machinery offers a range of products under its "many" Product System, which includes Vacuum Forming, Recycling Plastic, Sheet Film Line, Blow/Injection Molding Machine, EPE Foam Machine, Hydraulic Cutting Machine, Air Compressor/Screw Compressor, Chiller, Hopper Dryer, Crusher, Mixer, and Auto Loader. These products are part of the company's intelligent integrated system solutions for material feeding, air supply, water supply, and power supply, catering to the diverse needs of its customers.Champion Machinery's technical strength and supply chain advantages enable the company to efficiently meet customized demands and provide tailored solutions to its global customer base. With a strong commitment to innovation, quality, and customer satisfaction, Champion Machinery continues to be a trusted partner for businesses in the manufacturing industry.In conclusion, Champion Machinery's expansion into the global market with its high-quality PVC pipe production line reinforces the company's dedication to delivering advanced machinery solutions to its customers worldwide. With a focus on innovation, reliability, and customer service, Champion Machinery is well-positioned to meet the evolving needs of the international manufacturing industry and contribute to the success of businesses across different regions. For companies looking for efficient, reliable, and cost-effective PVC piping solutions, Champion Machinery's PVC pipe production line is a top choice.
New and Efficient Shredder for Processing Plastics and Foils - Model 2200
Title: Enhancing Recycling Efficiency: The Revolutionary Plastic Film ShredderIntroduction:As our society moves towards becoming more environmentally conscious, one of the most pressing challenges we face is managing the ever-increasing amount of plastic waste. Plastic films and foils, which are commonly used in packaging and other applications, contribute significantly to this problem. However, with the advent of the innovative Plastic Film Shredder, we now have a game-changing solution to process and recycle these materials efficiently. In this blog, we will explore the revolutionary WKS 2200 model, designed to address the plastic waste crisis and highlight the benefits of incorporating this shredder into recycling facilities.Understanding the Plastic Film Shredder:The WKS 2200 is the largest version available in the WKS series and represents a significant step forward in handling various plastics and foils. Suitable for processing plastic films and foils of all types, this model sets new industry standards for tackling plastic waste efficiently and sustainably. Combining advanced technologies with state-of-the-art engineering, the Plastic Film Shredder streamlines the recycling process, making it highly resourceful.Features and Benefits:1. Unmatched Capacity:With its large size, the WKS 2200 offers an unparalleled capacity for shredding plastic films of all kinds. Whether it's industrial plastic films, agricultural foils, or packaging materials, this shredder can handle high volumes of waste, reducing the need for manual labor and increasing overall productivity.2. Efficient Size Reduction:The precision cutting system featured in the WKS 2200 ensures consistent shredding results. By effectively reducing plastic films into smaller particles, this machine optimizes the recycling process and prepares the material for subsequent processing steps. The shredded plastics can be further used in the production of new plastic products, closing the recycling loop.3. Energy Optimization:Operating the Plastic Film Shredder involves minimal energy consumption. Thanks to its cutting-edge technology, this model prioritizes energy optimization by adopting advanced motor systems, resulting in significant cost savings for recycling facilities. This eco-friendly approach reduces the carbon footprint associated with waste processing.4. Versatility in Application:Apart from its primary use in the plastics and foils sector, the WKS 2200 can handle a wide range of materials. This versatile model is capable of shredding other recyclables such as paper, cardboard, textiles, and even wood waste. This flexibility makes it an ideal investment for recycling facilities seeking varied waste processing capabilities.5. Enhanced Safety and Durability:Constructed with utmost precision, the WKS 2200 ensures operator safety with innovative safety features and robust build quality. Equipped with advanced sensors and emergency shutdown systems, this shredder prioritizes the protection of workers and avoids potential accidents. Its long lifespan guarantees reliability and longevity, making it a valuable asset for recycling businesses.Conclusion:In the quest to combat the global plastic waste crisis, the Plastic Film Shredder - WKS 2200 model empowers recycling facilities with efficient and sustainable solutions. With its unparalleled capacity, optimized energy consumption, versatility in application, and emphasis on safety, this shredder revolutionizes the processing of plastic films and foils. By incorporating the WKS 2200 into existing recycling infrastructure, businesses can significantly contribute to reducing plastic waste while maximizing resource utilization. Let us embrace this game-changing technology and work towards a greener and more sustainable future.Keywords: Plastic Film Shredder, plastic waste, recycling efficiency, resource utilization, sustainability, WKS 2200, foils, packaging materials.
Top Injection Molding Manufacturer and Supplier in China - Factory Prices
Champion machinery, a leading manufacturer and supplier of injection molding machines and other plastic processing equipment, is making significant strides in the global market. As the company continues to expand its international presence, it has focused on building a strong network of agents and promoting its brand in various regions around the world.With a dedicated effort to explore new markets, Champion has established a global agent network that has been growing steadily. By actively engaging with customers in different countries, the company has been able to enhance its understanding of their specific needs and provide tailored solutions. Champion's commitment to face-to-face communication has played a crucial role in strengthening relationships with clients around the globe.One of Champion's core product offerings is the "many" Product System, which comprises a diverse range of equipment, including vacuum forming, recycling plastic, sheet film lines, blow/injection molding machines, EPE foam machines, hydraulic cutting machines, and various auxiliary equipment such as air compressors, screw compressors, chillers, hopper dryers, crushers, mixers, and auto loaders. These products are part of an intelligent integrated system that provides solutions for material feeding, air supply, water supply, and power supply, catering to the diverse needs of the plastic processing industry.Champion's technical expertise and robust supply chain enable the company to efficiently meet customized demands from clients. With a strong focus on innovation and quality, Champion machinery is well-positioned to deliver high-performance solutions to its global customer base.In addition to its product offerings, Champion is particularly known for its injection molding machines, which are designed to meet the demanding requirements of modern manufacturing. With a commitment to precision, reliability, and efficiency, Champion's injection molding machines have proven to be invaluable assets for a wide range of production applications.While Champion continues to expand its footprint globally, its core values of quality, reliability, and customer satisfaction remain unwavering. By prioritizing customer service and product excellence, Champion is poised to make a lasting impact in the international market.The company's efforts have not gone unnoticed, as it has garnered positive reviews from customers worldwide. With advanced technology, high precision, and optimal efficiency, Champion's injection molding machines have received acclaim for their exceptional performance and cost-effectiveness. Customers have highlighted the user-friendly nature of the machines, as well as their capability to handle a wide range of materials while delivering excellent quality finished products.As Champion continues to solidify its presence in Asia, Europe, Oceania, North and South America, Africa, and the Middle East, the company is well-positioned to become a leading global player in the plastic processing industry. With a strong focus on international expansion and a commitment to meeting the unique needs of customers in diverse markets, Champion machinery is poised for continued success on the global stage.
Affordable Second Hand Injection Moulding Machine in China - Best Deals!
Chinese Manufacturer Offers Quality Second Hand Injection Moulding Machines for Global MarketAs the global demand for manufacturing machinery continues to grow, Champion Machinery, a leading Chinese manufacturer, has stepped up to meet the needs of international markets by offering high-quality second hand injection moulding machines. With a strong focus on global expansion and localization, Champion Machinery has established a robust agent network and has been actively promoting its brand worldwide.Champion Machinery's commitment to customer service and international engagement is evident in their efforts to establish a strong presence in various regions, including Asia, Europe, Oceania, North and South America, Africa, and the Middle East. By engaging in face-to-face communication with customers overseas, Champion Machinery has been able to enhance mutual understanding and improve service delivery, solidifying their reputation as a trusted global partner in the manufacturing industry.The company's main products include a diverse range of equipment, collectively known as the "many" Product System. This system consists of six series of products, encompassing Vacuum Forming, Recycling Plastic, Sheet Film Line, Blow/Injection Molding Machines, EPE Foam Machines, Hydraulic Cutting Machines, and Air Compressor/Screw Compressor/Chiller/Hopper Dryer/Crusher/Mixer/Auto Loader, offering intelligent integrated system solutions for material feeding, air supply, water supply, and power supply. These offerings are designed to efficiently meet the customized demand based on the company's technical strength and supply chain advantages.Among the product series, Champion Machinery places special emphasis on its second hand injection moulding machines, recognizing the increasing demand for reliable and cost-effective machinery in the global market. The company takes pride in delivering quality equipment at competitive prices, ensuring that customers receive the best value for their investment.The second hand injection moulding machines offered by Champion Machinery are sourced from top manufacturers, guaranteeing high standards of quality and reliability. Prior to resale, each machine undergoes thorough testing and inspection to ensure optimal performance, providing customers with the peace of mind that they are acquiring durable and efficient machinery.By offering a range of sizes and capacities, Champion Machinery caters to diverse production needs, providing options for both small-scale and high-volume manufacturing. The company's extensive experience in the industry enables them to provide expert advice and support, guiding customers in selecting the right machine for their specific business requirements. In addition, Champion Machinery offers installation, training, and ongoing maintenance and repair services, ensuring a smooth transition into production and sustained operational efficiency.The decision to invest in a second hand injection moulding machine can be a strategic and cost-effective choice for businesses seeking to enhance their production capabilities. Champion Machinery's offering presents a reliable and efficient solution for manufacturing needs, enabling businesses to achieve their operational objectives without compromising on quality or affordability.In a global market characterized by evolving manufacturing demands, Champion Machinery's dedication to providing high-quality, cost-effective equipment positions them as an invaluable partner for businesses around the world. Their commitment to international expansion, customer engagement, and product excellence reflects their determination to meet the needs of a diverse and dynamic industry.For businesses considering the acquisition of second hand injection moulding machines, Champion Machinery stands out as a trusted and reputable supplier, offering a compelling combination of quality, reliability, and competitive pricing. Through their global outreach and comprehensive product range, Champion Machinery is well-positioned to support businesses seeking to optimize their manufacturing processes and achieve sustainable growth.Whether businesses are looking to invest in pre-owned machinery to expand their operations or to replace aging equipment, Champion Machinery's second hand injection moulding machines present a compelling opportunity to secure efficient, cost-effective, and durable solutions for their manufacturing needs. Contact Champion Machinery today to explore their selection of second hand injection moulding machines and discover how they can support your business's production capabilities.