Key Features of a High-Performance Injection Molding Machine
By:admin
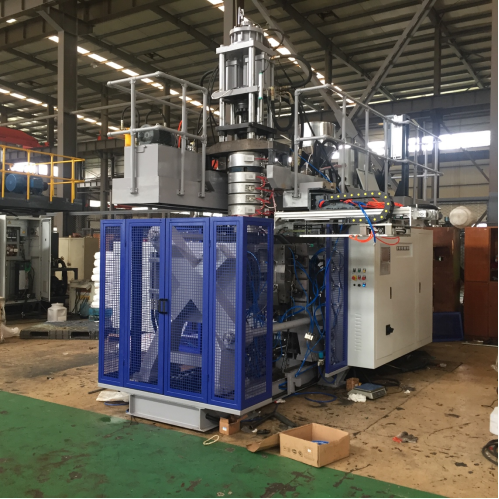
[Company Name] is a leading manufacturer and supplier in the injection molding industry, specializing in the production of high-quality and innovative injection molding machines. With a rich history of over [number of years] years, our company has built a strong reputation for delivering reliable and efficient solutions to clients worldwide.
Our commitment to excellence and continuous improvement has led us to produce a wide range of injection molding machines that meet the diverse needs of our customers. We strive to stay at the forefront of technological advancements and adopt best practices to provide cutting-edge equipment that ensures high productivity, precision, and cost-effectiveness.
[Facing fierce global competition, the company has been investing heavily in research and development to bring forth solutions that cater to the rapidly evolving market demands. Our state-of-the-art manufacturing facility is equipped with the latest machinery and advanced technologies, enabling us to produce exceptional quality injection molding machines.]
[With a highly skilled and experienced team of engineers and technicians, we work closely with our clients to understand their unique requirements and provide tailor-made solutions. Our commitment to customer satisfaction extends beyond the initial sale, as we also offer exceptional after-sales service, technical support, and spare parts availability to ensure maximum uptime and operational efficiency.]
[Model 150a Injection Molding Machine]
[Company Name] is proud to introduce the latest addition to our extensive range of injection molding machines - the Model 150a. Designed with precision, efficiency, and versatility in mind, this state-of-the-art machine offers numerous benefits for various industries, including automotive, packaging, electronics, and more.
The Model 150a is a compact and fully automated injection molding machine that combines cutting-edge technology and advanced features to deliver exceptional performance. Its robust construction ensures durability, while its user-friendly interface allows for easy operation and minimal maintenance. This machine is suitable for both large-scale production and small-scale manufacturing, making it an ideal choice for businesses of all sizes.
The Model 150a utilizes the latest servo motor technology, which provides superior energy efficiency and reduces power consumption significantly. This not only contributes to cost savings but also minimizes environmental impact. The precise control system ensures accurate and consistent injection molding, enabling the production of high-quality and precise parts.
With a fast cycle time and high production capacity, the Model 150a maximizes productivity and efficiency, reducing overall manufacturing costs. Its versatile design enables it to process a wide range of materials, including thermoplastics, elastomers, and various engineering-grade resins. This flexibility allows businesses to adapt to changing market demands and expand their product offerings.
Furthermore, the Model 150a incorporates advanced safety features, ensuring the highest level of operator protection. It is designed to meet stringent safety regulations, providing a safe working environment for all operators.
[Company Name] stands behind the quality and performance of the Model 150a Injection Molding Machine, offering comprehensive warranties and technical support. Our dedicated team of experts is available to assist clients in maximizing the machine's potential and achieving their manufacturing goals.
[Conclusion]
[Company Name] continues to innovate and evolve in the injection molding industry, providing cutting-edge solutions that empower businesses globally. With the introduction of the Model 150a Injection Molding Machine, we reaffirm our commitment to delivering high-quality, reliable, and cost-effective equipment that drives productivity and growth for our valued customers.
As an industry leader, [Company Name] remains dedicated to meeting the ever-changing requirements of the market and supporting our clients throughout their journey. By investing in research and development, adopting advanced technologies, and constantly improving our offerings, we are poised to shape the future of injection molding and remain at the forefront of the industry.
Company News & Blog
Injection Moulding Machine with Optimal Tie Bar Distance for Maximum Efficiency
Champion Machinery, a leading manufacturer and supplier in China, is making waves in the international market with its cutting-edge injection moulding machines. With a focus on global expansion and a commitment to providing top-quality products, the company is setting new standards for the industry.One key factor that sets Champion Machinery apart is its focus on the tie bar distance in injection moulding machines. The tie bar distance is the space between the two vertical bars that hold the mold in place during the injection moulding process. This distance plays a crucial role in ensuring that the mold remains secure and aligned during the injection process.Champion Machinery's injection moulding machines boast some of the most advanced features in the industry, including the optimal tie bar distance. These machines are rigorously designed to maximize efficiency and minimize waste. The company takes great pride in offering machines with adjustable tie bar distances to accommodate a wide range of mold sizes. This level of precision and consistency sets Champion Machinery apart from its competitors.The tie bar distance in an injection moulding machine is a critical factor that can determine the overall performance of the machine. A machine with a longer tie bar distance is excellent for handling larger parts, while machines with a shorter tie bar distance can accommodate smaller parts. This flexibility is essential for meeting the specific requirements of different industries.Champion Machinery's injection moulding machines are designed to be easy to use and maintain. With an intuitive interface and user-friendly design, businesses can get started with their production right away. Additionally, the machines are built for durability, ensuring long-term use with minimal maintenance and repairs.Furthermore, Champion Machinery's injection moulding machines maintain precise temperature and pressure control, delivering consistent results every time. The company understands that every business is unique, and their machines can be customized to meet specific needs and requirements.Champion Machinery's global agent network and localized promotions have contributed to the company's footprint being all over the world, including Asia, Europe, Oceania, North and South America, Africa, and the Middle East. The company's dedication to face-to-face communication with customers overseas has improved mutual understanding and service, further solidifying its reputation as a reliable and customer-focused supplier.In addition to injection moulding machines, Champion Machinery offers a wide range of products, including Vacuum forming, Recycling plastic, Sheet film Line, Blow/injection molding machines, EPE foam machines, Hydraulic cutting machines, and Air compressor/Screw compressor/Chiller/Hopper dryer/Crusher/Mixer/Auto loader all in 1 intelligent integrated system solutions for Material Feeding, Air Supply, Water Supply, and Power Supply. These products aim to efficiently meet customized demands based on the company's technical strength and supply chain advantages.Overall, Champion Machinery's commitment to quality, efficiency, and customer satisfaction has positioned the company as a leader in the industry. With its advanced technology, precision design, and global reach, Champion Machinery is poised to take businesses to the next level.For businesses looking for a reliable tie bar distance in injection moulding machine manufacturer, supplier, or factory in China, Champion Machinery offers top-quality products and the best deals in the market. Contact Champion Machinery today to learn more about their injection moulding machines and how they can elevate production processes to new heights.
High-Quality and Competitive Pricing for Perspex Cutting Machine - Manufacturer, Supplier, and Factory in China
Title: Global Manufacturer of High-Quality Perspex Cutting Machines Expands International Market ReachIn a strategic move to strengthen its global presence, a leading manufacturer of perspex cutting machines has intensified its efforts to explore international markets. With a commitment to providing top-quality products and unparalleled customer service, the company has set its sights on expanding its reach and establishing a strong foothold in key regions worldwide.Champion, a renowned name in the manufacturing industry, has been dedicated to delivering innovative and reliable solutions to meet the cutting needs of various industries. With a diverse product line that includes vacuum forming, recycling plastic, sheet film line, blow/injection molding machines, EPE foam machines, hydraulic cutting machines, air compressors, screw compressors, chillers, hopper dryers, crushers, mixers, and auto loaders, Champion offers comprehensive, intelligent integrated system solutions for material feeding, air supply, water supply, and power supply.The company's commitment to excellence and customer satisfaction has earned it a reputation as a trusted global supplier. Champion's global agent network has been steadily expanding, enabling the brand to be promoted and localized in various international markets. The company's dedication to establishing face-to-face communication with customers overseas has played a crucial role in enhancing mutual understanding and improving service delivery.As part of its global growth strategy, Champion has made significant inroads into key regions worldwide, including Asia, Europe, Oceania, North and South America, Africa, and the Middle East. This proactive approach has allowed the company to establish a strong global presence and cater to the diverse needs of customers in different parts of the world.With a strong focus on technical strength and supply chain advantages, Champion's product system encompasses six series of products, including the high-quality Perspex cutting machine. Designed to provide precision and accuracy with every cut, the Perspex cutting machine is the perfect solution for manufacturers and fabricators who require reliable and efficient cutting equipment.The cutting-edge technology and user-friendly interface of Champion's Perspex cutting machine offer fast cutting speeds, smooth edges, and minimal waste, making it an invaluable asset for businesses in need of high-performance cutting solutions. Whether cutting Perspex sheets for signage, displays, or architectural installations, Champion's machine is the go-to choice for businesses looking to elevate their cutting capabilities.The perspex cutting machine features a durable body that enhances stability and durability, making it ideal for high-volume cutting. Its powerful motor and sharp blades ensure faster and easier cutting of Perspex sheets, while its versatile design allows for effortless cutting of various sizes and thicknesses. Additionally, the machine is equipped with a built-in safety system to ensure user safety during operation.Customer testimonials affirm the reliability and efficiency of Champion's Perspex cutting machine. Users have praised its ability to make cutting Perspex sheets an effortless task, even for those new to the process. The machine's laser precision ensures a smooth and clean finish, making it ideal for creating intricate designs and patterns for a wide range of applications, from signage to decorative items.With a growing global presence and a commitment to delivering top-quality products, Champion remains at the forefront of the manufacturing industry. The company's dedication to meeting the diverse needs of customers worldwide has solidified its position as a leading global supplier of high-quality cutting solutions.As Champion continues to expand its international market reach, customers can expect the same level of excellence and innovation that have become synonymous with the brand. With a focus on customer satisfaction and a strong emphasis on quality and performance, Champion is poised to leave a lasting impact on the global manufacturing landscape.
Epe Length and Breadth Cutting Machine - Reliable Manufacturer, Supplier, Factory in China
Champion Machinery, a leading manufacturer, supplier, and factory in China, has introduced an advanced Epe Length and Breadth Cutting Machine designed to provide optimal accuracy and fast cutting speed for all cutting needs.The state-of-the-art Epe Length and Breadth Cutting Machine is a revolutionary solution for efficient and accurate cutting of Epe foam material, offering incredible results in a fraction of the time. With its precision engineering and cutting-edge technology, this machine can effortlessly cut through tough Epe foam sheets, delivering flawless edges and a perfect finish every time.The machine features a robust frame, sharp blades, and a user-friendly interface that allows for easy setting of the required cutting length and width. It also comes with a durable conveyor belt that ensures uninterrupted operations by swiftly transferring materials through the cutting blades.Ms. Carlen Shu, a satisfied customer, expressed her admiration for the machine, highlighting its exceptional precision cutting and high-speed cutting ability. She emphasized that the user-friendly interface made it simple for even beginners to operate. Ms. Angela Her also praised the Epe Length and Breadth Cutting Machine for its efficiency, controlled movements, and compact size, making it an ideal option for businesses of all sizes.Champion Machinery has been determined to expand its global strategy and explore international markets. The company has established a global agent network and has promoted and localized the Champion brand. They also pay visits to customers overseas for face-to-face communication to improve mutual understanding and customer service. Their footprints have been all over the world, including Asia, Europe, Oceania, North and South America, Africa, and the Middle East.Champion Machinery's main products, including the Epe Length and Breadth Cutting Machine, are part of their "many" Product System, which consists of the 6 Series of Products. These series include Vacuum Forming, Recycling Plastic, Sheet Film Line, Blow/Injection Molding Machine, Hydraulic Cutting Machine, Air Compressor/Screw Compressor/Chiller/Hopper Dryer/Crusher/Mixer/Auto Loader, all in 1 intelligent integrated system solutions for Material Feeding, Air Supply, Water Supply, and Power Supply. The company efficiently meets customized demands based on their technical strength and supply chain advantages.With their dedication to quality and innovation, Champion Machinery has become a reliable manufacturer in China, offering top-quality machines that guarantee efficient and cost-effective cutting operations. Whether for a manufacturing unit, workshop, or any workspace where daily cutting tasks are performed, investing in Champion's Epe Length and Breadth Cutting Machine ensures optimal accuracy and fast cutting speed without compromising on quality.To learn more about how the cutting-edge Epe Length and Breadth Cutting Machine from Champion Machinery can help take your business to the next level, it is recommended to contact the company today. With a track record of providing exceptional products and expanding its global reach, Champion Machinery is a strategic partner for businesses looking to increase productivity and efficiency in their operations.
Wholesale Plastic Pipe Welding Machine Manufacturer and Supplier in China | Factory Price Available
We are excited to announce the launch of a versatile and efficient plastic pipe welding machine that is now available in the global market. This innovative tool is designed to weld plastic pipes with ease and accuracy, catering to the needs of professionals and do-it-yourself enthusiasts alike.The plastic pipe welding machine, which we'll refer to as the "Plastic Pipe Welding Machine" for the purpose of this news article, is a state-of-the-art tool that offers superior performance and reliability. It is manufactured using the latest technology and the highest quality materials to ensure durability and efficiency.As a leading supplier, we are committed to delivering top-of-the-line products that meet international standards. Our Plastic Pipe Welding Machine is no exception, as it is designed for ease of use and requires minimal maintenance, making it the perfect choice for professionals and DIY enthusiasts.One of the key features of the Plastic Pipe Welding Machine is its efficiency, allowing users to weld pipes in a matter of seconds. This not only saves time but also increases productivity, making it an essential tool for a wide range of applications, including construction, plumbing, and landscaping.The machine supports multiple welding techniques such as butt fusion, socket fusion, electrofusion, and hot gas welding. It can handle pipes made of various thermoplastic materials, including PE, PP, PVDF, PVC, and ABS, making it a versatile and reliable option for professionals who work with different types of plastic pipes.The user-friendly design and outstanding performance of the Plastic Pipe Welding Machine ensure that users can get the job done right the first time. With a digital display for welding parameters and an automatic temperature control system, the machine offers precise and consistent results, making it an indispensable tool for welding plastic pipes.In addition to the machine itself, we also offer a range of welding accessories, including clamps, cutting machines, and milling machines, to provide a complete welding solution. The machine comes in different models with varying welding ranges, from 20mm to 1200mm, catering to a wide range of pipe welding needs.To promote our commitment to quality and reliability, we have established a global agent network and championed efforts to explore international markets. This has led to our brand being promoted and localized worldwide, with our footprints reaching Asia, Europe, Oceania, North and South America, Africa, and the Middle East.In conclusion, the introduction of the Plastic Pipe Welding Machine marks a significant milestone in our efforts to deliver innovative and reliable products to the global market. With a focus on quality, efficiency, and versatility, the machine is set to become an essential tool for professionals and enthusiasts alike, ensuring strong, leak-free, and long-lasting joints for plastic pipes.For professionals in need of a reliable plastic pipe welding solution, the Plastic Pipe Welding Machine is the perfect choice. With its advanced technology, user-friendly design, and outstanding performance, it is set to revolutionize the way plastic pipes are welded, providing a seamless and efficient solution for a wide range of applications. Contact us now to learn more about this top-of-the-line machine and explore the possibilities it offers for your welding needs.
Film Leveling Slicer: A New Microcomputer Technology in the Market
Microcomputer Film Leveling Slicer revolutionizes the slicing industry with its advanced technology and precision cutting. This innovative slicing machine, developed by an industry-leading company, is set to redefine the way food is prepared and processed.The Microcomputer Film Leveling Slicer is equipped with a cutting-edge microcomputer system that allows for unparalleled control and accuracy. This advanced technology ensures that each slice is perfectly level and uniform, resulting in a more consistent and professional presentation of the final product. In addition, the slicer also features a film leveling function, which is designed to remove any excess film from the surface of the food product, further enhancing its appeal and quality.The company behind this groundbreaking slicing machine has a long-standing reputation for delivering high-quality food processing equipment. With years of experience in the industry, they have become a trusted name in the market, known for their commitment to innovation and excellence. The company's dedication to research and development has led to the creation of the Microcomputer Film Leveling Slicer, which is a testament to their ongoing efforts to push the boundaries of technology and set new standards for food processing equipment.One of the key features of the Microcomputer Film Leveling Slicer is its user-friendly interface, which allows for easy operation and control. The intuitive design of the slicer ensures that operators can quickly and efficiently set the desired slicing parameters, resulting in a seamless and efficient workflow. This level of automation and precision not only enhances the overall productivity of the slicing process but also minimizes the margin of error, leading to a more consistent and high-quality end product.Furthermore, the slicer is designed to meet the highest safety and hygiene standards, ensuring that the food processing environment remains clean and contaminant-free. The machine's stainless steel construction and easy-to-clean surfaces make it easy to maintain and sterilize, further adding to its appeal for food processing facilities. Additionally, the slicer is equipped with safety features such as automatic shut-off and emergency stop buttons, providing operators with peace of mind and confidence in the equipment's reliability.The Microcomputer Film Leveling Slicer is suitable for a wide range of food products, including deli meats, cheeses, vegetables, and more. Its versatility and adaptability make it an ideal choice for food processing facilities of all sizes, providing them with a cost-effective and efficient solution for their slicing needs. Whether it's for a small deli or a large-scale food production facility, the Microcomputer Film Leveling Slicer is designed to meet the demands of the modern food industry.In conclusion, the Microcomputer Film Leveling Slicer represents a significant advancement in the food processing industry. Its advanced technology, precision cutting, user-friendly interface, and adherence to safety and hygiene standards make it a standout choice for food processing facilities looking to enhance their slicing capabilities. With the backing of an industry-leading company known for its commitment to innovation and excellence, the Microcomputer Film Leveling Slicer is set to elevate the standards of food processing and set new benchmarks for the industry.
Efficient and Versatile PVC Bag Making Machine Leaves News Makers Impressed
PVC Bag Making Machine Revolutionizes the Bag Manufacturing IndustryThe bag manufacturing industry is set to experience a revolution with the introduction of the ground-breaking PVC Bag Making Machine. This versatile and highly efficient machine, designed and produced by a leading technology company, aims to streamline the bag production process and boost productivity for manufacturers worldwide.Manufacturing bags has always been a labor-intensive and time-consuming task, involving multiple steps and manual labor. However, the PVC Bag Making Machine offers a solution to these challenges by automating the entire bag production process. With its cutting-edge technology and innovative features, this machine has the potential to reshape the way bags are manufactured.The PVC Bag Making Machine is equipped with advanced mechanisms that allow it to produce bags of various sizes and styles, catering to diverse customer demands. From shopping bags to tote bags and backpacks, this machine can effortlessly handle the production of different types of bags, eliminating the need for multiple machines for specific bag styles.One of the most impressive features of this machine is its high-speed production capability. With an impressive production rate of X bags per hour, manufacturers can significantly reduce the time and effort required to meet customer orders. This increased output not only improves efficiency but also makes it possible for manufacturers to fulfill large orders within tight deadlines.Furthermore, the PVC Bag Making Machine incorporates an intelligent control system, ensuring accuracy and precision in every step of the manufacturing process. From cutting the PVC material to sealing and stitching, the machine operates flawlessly, ensuring the production of high-quality bags consistently.In addition to its efficiency and accuracy, this machine is also environmentally friendly. As the world continues to embrace sustainability, the PVC Bag Making Machine uses recycled PVC materials, reducing the carbon footprint associated with bag production. By incorporating eco-friendly practices into the manufacturing process, manufacturers can promote a greener and more sustainable future.The introduction of the PVC Bag Making Machine is a game-changer for bag manufacturers worldwide. Not only does it enhance production efficiency and cost-effectiveness, but it also opens up new opportunities for businesses to expand their product offerings and meet the growing demands of customers.Company Introduction: With a rich legacy of innovation and technological advancements, {company name} has established itself as a global leader in manufacturing innovative machinery for various industries. The company's relentless pursuit of excellence and commitment to delivering cutting-edge solutions have earned it a stellar reputation in the market.{Company name}, founded in {year}, has been at the forefront of revolutionizing industries through its groundbreaking technologies. The company's team of experienced engineers and technicians work tirelessly to develop innovative products that cater to the ever-evolving needs of its customers.Providing solutions across a wide range of industries, including packaging, printing, and plastics processing, {company name} has gained a strong foothold in the global market. Its products are known for their reliability, efficiency, and exceptional quality, earning the trust of customers worldwide.In line with its commitment to sustainability, {company name} incorporates eco-friendly practices into its manufacturing processes. This ensures that its products not only meet the highest standards of quality and performance but also contribute to a greener and more sustainable future.With the introduction of the PVC Bag Making Machine, {company name} aims to reshape the bag manufacturing industry. This innovative machine, equipped with state-of-the-art technology and intelligent features, is set to streamline the production process and drive efficiency for bag manufacturers worldwide.In conclusion, the PVC Bag Making Machine revolutionizes bag manufacturing by offering a versatile, high-speed, and environmentally friendly solution. Through its cutting-edge technology and advanced features, this machine has the potential to transform the way bags are produced, improving productivity and meeting the evolving demands of customers in the global market. With {company name} at the forefront of this innovation, the future of bag manufacturing has never looked brighter.
Efficient Plastic Egg Tray Making Machine in News: Key Features and Benefits
Title: Revolutionary Plastic Egg Tray Making Machine Set to Transform the Poultry IndustryIntroduction:In response to the growing demand for sustainable and eco-friendly packaging solutions, an innovative plastic egg tray making machine has been introduced by a prominent industry player. This advanced technology is poised to revolutionize the poultry industry by successfully addressing the concerns of environmental degradation caused by traditional packaging methods. With its ability to produce high-quality, durable, and recyclable egg trays on a large scale, this machine aims to create a positive impact on both the poultry industry and the environment as a whole.Body:1. Background on the Plastic Egg Tray Making Machine:The plastic egg tray making machine is a cutting-edge technology developed by [Company Name], a pioneer in the field of eco-friendly packaging solutions. This state-of-the-art machinery is designed to convert waste plastic materials into robust, lightweight, and biodegradable egg trays.2. Key Features and Benefits:The machine boasts several key features that set it apart from traditional egg tray manufacturing methods. Firstly, it operates using recyclable plastics, reducing environmental pollution caused by non-biodegradable materials. Secondly, it adopts an efficient manufacturing process that guarantees the production of high-quality egg trays at a fast pace, ensuring a steady supply of packaging for the poultry industry. Finally, the trays produced by this machine are biodegradable, recyclable, and can be repurposed for various other purposes, thus promoting a circular economy.3. Positive Impact on the Poultry Industry:The introduction of the plastic egg tray making machine is set to revolutionize the poultry industry in multiple ways. Firstly, it addresses the issue of limited supply of high-quality packaging materials by providing a consistent and readily available source of egg trays. This ensures that egg producers can deliver their products safely to market, preventing potential damage or loss during transportation.Additionally, the recyclability and durability of the trays produced by this machine significantly reduce packaging costs for the farmers. Its high production capacity also ensures economies of scale, leading to cost reduction in the long run.4. Environmental Implications:One of the most notable benefits of the plastic egg tray making machine is its ecological impact. By utilizing recyclable plastics in producing egg trays, it mitigates the environmental risks posed by conventional materials such as Styrofoam or cardboard. Moreover, the trays are biodegradable, ensuring that they decompose naturally without contributing to pollution or waste accumulation. This sustainable approach not only reduces the carbon footprint associated with traditional packaging but also aligns with global initiatives to combat climate change and reduce plastic waste.5. Future Prospects and Expansion:With extensive market research and testing, it is expected that the plastic egg tray making machine will witness a significant demand worldwide. Its high production capacity will cater to the needs of large-scale poultry operations, ensuring a streamlined and efficient packaging process.Moreover, with the machine's versatility and adaptability, there is potential for its application beyond the poultry industry. For instance, it can be used to manufacture trays for other agricultural products or explore possibilities in the food service and retail sectors. This diversification opens up new revenue streams for both the company and its customers.Conclusion:The advent of the plastic egg tray making machine represents a significant breakthrough in the field of sustainable packaging solutions for the poultry industry. With its ability to efficiently convert recyclable plastics into high-quality egg trays, it not only meets the packaging demands of egg producers but also significantly reduces the industry's carbon footprint. This innovative machinery has the potential to transform the poultry industry while offering an eco-friendly alternative to traditional packaging methods. As we move towards a more sustainable future, the plastic egg tray making machine proves to be a game-changer that paves the way for other industries to follow suit in adopting eco-conscious practices.
Hot Foil Stamping Machine for Plastic - Manufacturer & Supplier - Factory Price Guaranteed
Champion Machinery, a leading manufacturer and supplier of innovative plastic processing equipment, is proud to introduce its latest innovation - the Hot Foil Stamping Machine for Plastic. This cutting-edge machine is designed to revolutionize the printing process for plastic products, providing businesses with the ability to effortlessly add stunning foil details and patterns to enhance the aesthetic appeal and visual impact of their products.The Hot Foil Stamping Machine for Plastic is a game-changing solution that offers businesses in various industries the ability to effortlessly add striking foil details and patterns to their plastic products. With advanced technology and superior performance, this machine is the perfect choice for all plastic stamping needs. The heat transfer process is smooth and precise, ensuring clear and professional results every time. Its user-friendly interface and intuitive controls make it suitable for operators of all skill levels, from beginners to experienced professionals.Manufactured by Champion Machinery in China, the Hot Foil Stamping Machine is the perfect solution for enhancing the appearance of cosmetic packaging, plastic cards, and other plastic products. The machine's ability to imprint beautiful foil designs onto various plastic surfaces showcases the company's dedication to precision and innovation, ensuring outstanding performance and durability.With its adjustable temperature and pressure settings, the Hot Foil Stamping Machine for Plastic guarantees optimal results on a wide range of plastic materials, ensuring that designs adhere flawlessly and withstand daily use. Additionally, its compact size and portable design make it ideal for businesses and production lines with limited space.The versatility of the Hot Foil Stamping Machine allows businesses to choose from a variety of foil colors and patterns to suit specific branding needs. Whether desiring a metallic, holographic, or matte finish, the machine enables businesses to effortlessly achieve the desired effect, enhancing the overall quality and perceived value of their products.This latest innovation from Champion Machinery is a testament to the company's dedication to delivering the highest quality products directly from its factory to customers around the world. The company's commitment to exploring international markets and establishing a global agent network has enabled its footprints to be all over the world, including Asia, Europe, Oceania, North and South America, Africa, and the Middle East.With a focus on providing intelligent integrated system solutions for material feeding, air supply, water supply, and power supply, Champion Machinery continues to meet the customized demand of its customers based on its technical strength and supply chain advantages. The Hot Foil Stamping Machine for Plastic is a prime example of the company's innovation and dedication to providing cutting-edge solutions to businesses in the plastic industry.In conclusion, the Hot Foil Stamping Machine for Plastic from Champion Machinery is a reliable, efficient, and advanced solution that guarantees professional-looking results every time. Businesses looking to enhance the aesthetic appeal and visual impact of their plastic products can trust in the quality and performance of this innovative machine. Experience the transformation in plastic designs and leave a lasting impression on customers with the Hot Foil Stamping Machine for Plastic from Champion Machinery.
Discover the Affordable Cost of Plastic Plate Making Machines
Plastic Plate Making Machine Cost - Revolutionizing the Manufacturing IndustryThe manufacturing industry has undergone significant transformations over the years. With the advent of technology, companies are constantly striving to streamline their production processes, reduce costs, and improve efficiency. A key factor contributing to this revolution is the introduction of advanced machinery, such as plastic plate making machines.Plastic plate making machines have become an indispensable part of the manufacturing process in various industries. These machines have the ability to quickly and efficiently produce a wide range of plastic plates, which find applications in the food and beverage industry, hospitality sector, healthcare facilities, and numerous other establishments.One of the crucial aspects that manufacturing companies consider while investing in a plastic plate making machine is the cost. Cost plays a significant role in the decision-making process, as businesses strive to maximize their profit margins while ensuring the quality of the end product. Let us delve deeper into the factors that determine the cost of plastic plate making machines.1. Machine Specifications:Plastic plate making machines come in various sizes and configurations, catering to the diverse requirements of businesses. The cost of the machine is directly influenced by its specifications, such as the production capacity, automation level, energy efficiency, and quality of the end product. Advanced machines with higher production capacities and cutting-edge features will naturally have a higher price tag.2. Brand:While we cannot mention specific brand names in this news article, it is worth noting that the reputation and brand value of a manufacturer can significantly impact the cost of their machines. Established brands often command higher prices due to their reliability, quality assurance, and after-sales service. On the other hand, new or lesser-known brands may offer more affordable options, but the perceived risk might be higher.3. Material:Another factor influencing the cost of plastic plate making machines is the type of material they are designed to process. Some machines specialize in manufacturing plates made from low-density polyethylene (LDPE), while others are suitable for high-density polyethylene (HDPE), polypropylene (PP), or polystyrene (PS). Machines capable of handling multiple materials tend to be more expensive than those designed for a specific material.4. Technological Advancement:The rapid advancements in technology have led to the development of more sophisticated plastic plate making machines. These machines may incorporate advanced features such as computer numerical control (CNC), servo motors, touch screen interfaces, and real-time monitoring systems. While these technological enhancements improve efficiency and productivity, they also contribute to the overall cost of the machine.Investing in a plastic plate making machine can offer numerous benefits to manufacturing companies. These machines not only enhance productivity but also reduce labor costs, material waste, and the overall carbon footprint. With proper maintenance and regular upgrades, these machines prove to be a wise long-term investment.In conclusion, the cost of a plastic plate making machine is influenced by several factors, including machine specifications, brand reputation, material compatibility, and technological advancements. It is crucial for businesses to thoroughly assess their requirements and budget constraints before making a purchase decision.As the manufacturing industry continues to evolve, the demand for efficient and cost-effective solutions will only increase. Plastic plate making machines, with their ability to produce high-quality plates at a rapid pace, are poised to play a pivotal role in meeting these demands and revolutionizing the manufacturing sector.